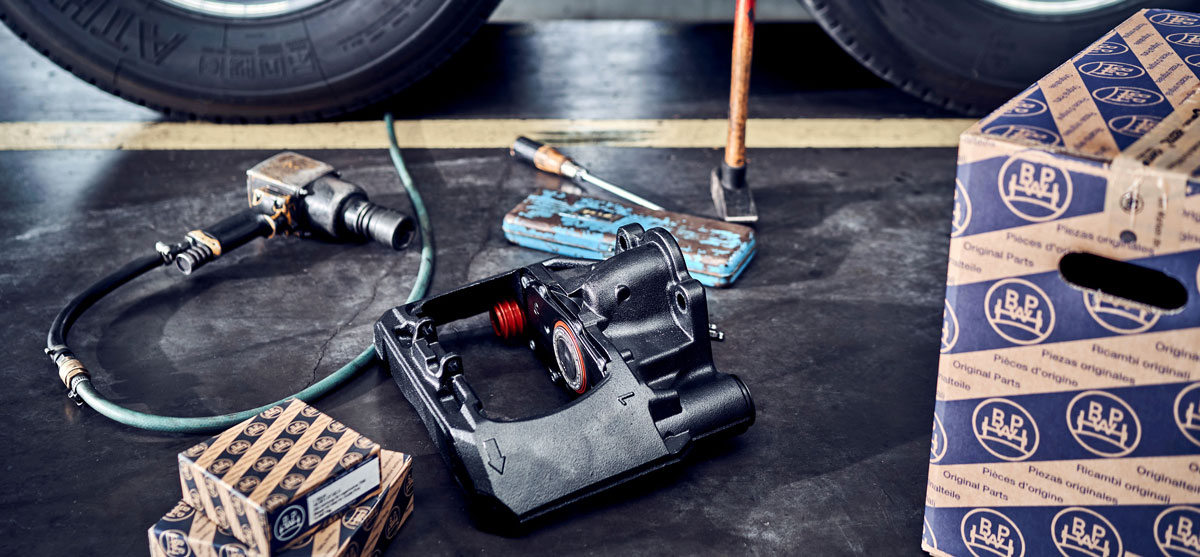
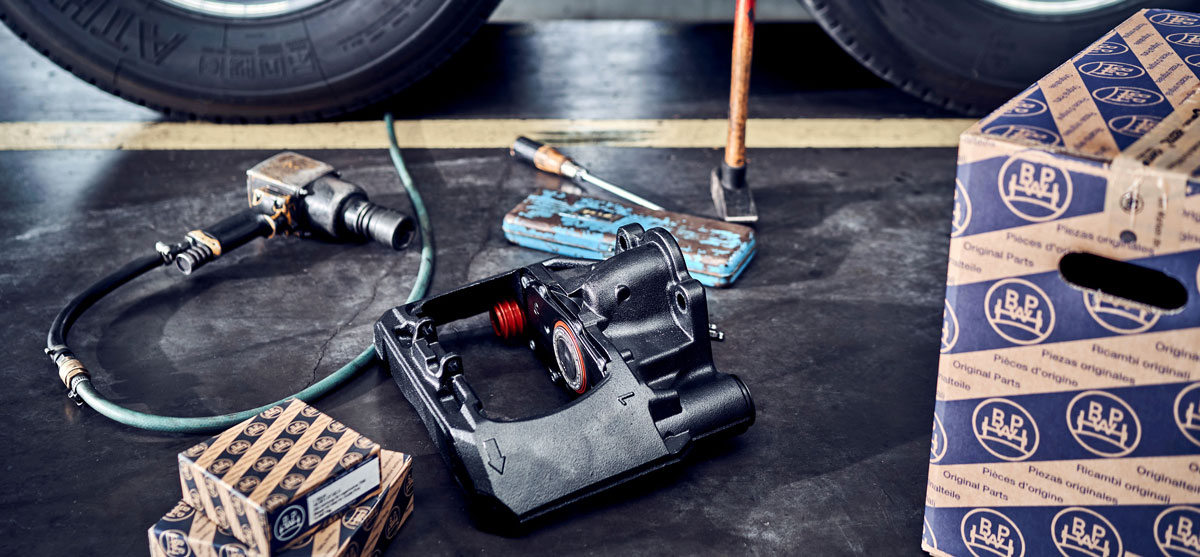
Remanufacturing – ein zweites Leben
Remanufacturing, Wiederaufbereitung, Aufarbeitung oder kurz ‚Reman‘, ist ein Thema, welches in der Nutzfahrzeugbranche zunehmend an Bedeutung gewinnt. Nicht nur bei der zeitwertgerechten Reparatur, sondern insbesondere auch was die Bestrebungen angeht, den Energie- und Ressourcenverbrauch zu reduzieren und die gesteckten Klimaziele zu erreichen. Aufgearbeitete Komponenten spielen hierbei eine wichtige Rolle.
Je älter ein Lkw oder Trailer ist, desto mehr stellt sich bei der Reparatur die Frage: Lohnt sich der Austausch eines defekten Fahrzeugteils durch ein neues Ersatzteil noch? Weil diese Frage in Zeiten angespannter wirtschaftlicher Rahmenbedingungen zunehmend in den Fokus rückt, setzen immer mehr OE-Hersteller neben ihren OES-Produkten auf preisgünstigere und dennoch qualitativ hochwertige Alternativen. Stichwort: ‚Zeitwertgerechte Reparatur‘. Viele Erstausrüster haben deshalb speziell für ‚besonders wettbewerbsgefährdete‘ Ersatzteile eine zweite Teilelinie etabliert. Hinter dieser Zweitmarke können sowohl Ident-Teile, also bau- sowie funktionsgleiche Neuteile stecken, die nach den Vorgaben des OE-Herstellers produziert werden, oder sogenannte Reman-Teile. Dabei steht ‚Reman‘ für remanufactured, also wiederaufbereitet.
Beide Alternativen sind deutlich preisgünstiger als das entsprechende Original-Serviceteil, ohne dass der Kunde bei Qualität und Sicherheit Abstriche machen muss. Die Aftermarkt-Sparte ‚TruckServices‘ von Knorr-Bremse beispielsweise hat für die angebotenen Reman-Parts mit ‚EconX‘ sogar eine eigene Produktmarke aufgelegt. Ziel dieser Mehr-Linien-Ersatzteilstrategien der OE-Hersteller ist es offensichtlich, mit den ebenfalls immer stärker werdenden Handels-, Haus- und Eigenmarken des Teilegroßhandels konkurrieren zu können.
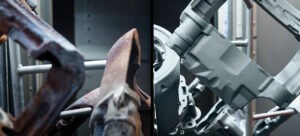
Nachhaltig und ressourcenschonend
Das Thema ‚Reman‘ gefällt aber nicht nur durch eine interessante Preisgestaltung, es schont auch die Umwelt und spart Ressourcen. Ein Argument, das angesichts des CO2-Footprints, der Klimaziele sowie der Rohstoffverknappung nicht nur bei den Ersatzteilherstellern selbst, sondern auch bei deren Kunden zieht.
Dabei handelt es sich laut einer Sprecherin von ZF beim Remanufacturing „um ein kontrolliertes und nachhaltiges industrielles Aufarbeitungsverfahren, bei dem bereits gebrauchte Produkte oder Teile wieder in einen Zustand gebracht werden, der sowohl bezüglich Qualität, als auch Leistung neuwertig oder sogar besser als neu ist. Dieses Verfahren erlaubt den Produkten mehrere Lebenszyklen zu durchlaufen und bietet erhebliche Zeit-, Material- und Kosteneinsparungen im Vergleich zur komplett neuen Herstellung eines Aftermarket-Produkts.“
Ähnlich formuliert es ein Sprecher von Knorr-Bremse: „Aufbereitete Produkte unserer Marke ‚EconX’ sind besonders geeignet für ältere Nutzfahrzeuge. Hier spricht man von einer ‚lebensdaueroptimierten Reparaturlösung zur Verbesserung der TCO für die Besitzer dieser Fahrzeuge’.” EconX-Produkte sind um bis zu 20 Prozent günstiger als Service-Neuteile.
Ein Wachstumsmarkt
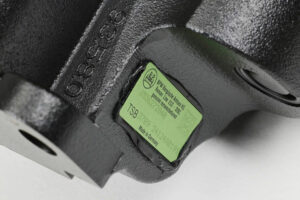
Das Geschäft mit wiederaufbereiteten Teilen wächst. Neben den OE-Herstellern selbst und den von den Herstellern zertifizierten und beauftragten Reman-Spezialisten, gibt es immer mehr freie ‚Universal-Aufbereiter‘. Während die OE-Hersteller nahezu unisono nur ihren eigenen Produkten ein weiteres Leben verleihen, wagen sich Universal-Aufbereiter nahezu an alles, was sich im Sinne der zeitwertgerechten Reparatur vermarkten lässt. Entsprechend groß – und unübersichtlich (speziell im Internet!) – ist mittlerweile das Angebot. Sowohl, was die Produktvielfalt, als auch die Produktqualität betrifft.
Einige Unterschiede sind schon auf den ersten Blick offensichtlich, etwa was den Korrosionsschutz angeht. Kommt bei höherpreisigen OE-Komponenten meist ein langlebiger, chemischer Oberflächenschutz zum Einsatz, müssen sich preisgünstigere Produkte mit einer simplen Lackierung begnügen. Die wesentlichen Unterschiede verbergen sich allerdings im Inneren der aufgearbeiteten Bauteile, und zwar in Form und Anzahl der beim Reman-Prozess erneuerten Komponenten. Während bei OE-Reman-Produkten üblicherweise Original-Ersatzteile verbaut werden, bedienen sich Universal-Aufbereiter durchaus auch bei anderen Quellen. Vielfach werden auch mehr der ursprünglichen Teile (teils unangetastet) wiederverwendet. Beides hat nicht nur Auswirkungen auf den Preis, sondern den OE-Herstellern zufolge möglicherweise auch auf die Funktionssicherheit und Lebensdauer der jeweiligen Komponente.
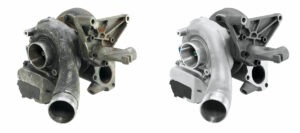
Vielfältiges Angebot
Das Angebot wiederaufbereiteter Teile ist mittlerweile enorm und es wächst kontinuierlich weiter. Typische Reman-Komponenten sind unter anderem:
- Zuspanneinheiten (Bremssättel)
- Federspeicherzylinder
- Module für elektronische Bremssysteme (EBS): Drucksteuermodule, Fußbremsmodule, Anhänger-Steuermodule
- Kompressoren für die Luftaufbereitung (Luftpresser)
- Klimakompressoren
- Turbolader und Abgasrückführ (AGR)-Ventile und -Kühler
- Kardanwellen
- Module für die elektronische Luftaufbereitung (EAC)
- Ölabscheidungspatronen (OSC)
- Motorsteuergeräte.
Deutliche CO2-Einsparung
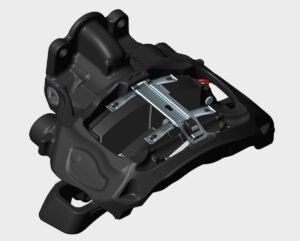
Branchenexperten zufolge ist industrielles Aufarbeiten die höchste Art von Recycling. Durch das Remanufacturing von Altprodukten lassen sich nämlich wertvolle Rohstoffe und teure Energie einsparen: Statt nur das Material von Altprodukten stofflich zu recyceln, werden die noch funktionstüchtigen Teile aufgearbeitet, neu montiert und wiederverwendet. Laut ZF lassen sich bei der Aufarbeitung von gebrauchten Fahrzeugteilen gemäß dem Serienstandard bis zu 90 Prozent der Rohstoffe einsparen, welche für die Herstellung eines Neuteils notwendig sind. Ein weiteres Argument pro ‚Reman‘ sind die eingesparten CO2-Emissionen. Wie hoch die erzielbare Einsparung ist, hängt dabei stark vom jeweiligen Bauteil und dem erforderlichen Produktions- beziehungsweise Wiederaufarbeitungsaufwand ab.
Einer theoretischen Beispielrechnung von BPW zufolge lassen sich bei der Fertigung von 10.000 Bremssätteln der ‚BPW Reman Line‘ bis zu 367 Tonnen CO2 einsparen. Ähnlich sieht die von Knorr-Bremse aufgemachte Rechnung für die Herstellung einer ‚EconX‘-Zuspanneinheit des Typs SN7 aus. Durch die Verwendung gebrauchter Komponenten fallen pro Einheit bis zu 44,9 kg weniger CO2-äquivalente Emissionen an. Über alle Produktreihen hinweg hat Knorr-Bremse nach eigenem Bekunden im Jahr 2023 durch Remanufacturing in Europa 3.648 Tonnen CO2, 1.220 Tonnen Material und 18,97 MWh Energie eingespart. Auch die von ZF für das Jahr 2022 ausgewiesenen Zahlen lesen sich beeindruckend. Demnach wurden durch Remanufacturing konzernweit mehr als 32.000 Tonnen CO2-Emissionen vermieden.
Remanufacturing statt Reparatur
Professionelles Remanufacturing ist deutlich mehr als nur eine fachgerechte Reparatur. Bei einer Reparatur zerlegt die Werkstatt ein Produkt soweit wie nötig, richtet oder ersetzt das schadhafte Einzelteil und macht so das Fahrzeug wieder flott. Die Gewährleistung bezieht sich lediglich auf die bei der Reparatur eingesetzten Neuteile sowie die geleistete Arbeit. Bei der industriellen Wiederaufbereitung dagegen wird das gebrauchte Produkt komplett zerlegt, Verschleißteile werden entsorgt, alle übrigen Einzelteile nach industriellen Prozess-Standards gereinigt, überprüft und wenn nötig aufgearbeitet. Bei der anschließende Wiedermontage kommen Original-Ersatzteile zum Einsatz und die Qualitätssicherung entspricht der Neuteilefertigung – weshalb derart aufgearbeitete Produkte die volle gesetzliche Gewährleistung besitzen.
Der eigentliche Reman-Prozess
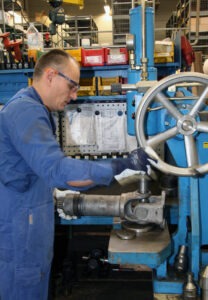
Die industrielle Aufarbeitung ähnelt stark der Herstellung von Neuprodukten und findet bei den meisten OE-Herstellern sogar auf den gleichen Fertigungsanlagen statt. Dennoch gibt es einen entscheidenden Unterschied: Anders als beim Neuprodukt stammt ein gewisser Prozentsatz der Einzelteile von der gebrauchten Komponente. Da OE-Hersteller nahezu ausnahmslos nur eigene Produkte aufarbeiten, sind die Prozesse jeweils speziell auf die betreffende Komponente abgestimmt.
Obschon jeder Aufbereiter seine eigenen Abläufe und Standards definiert, ähneln sich die Reman-Prozesse in den wesentlichen Punkten, speziell in der OE-Schiene. Der erste Prozessschritt ist die Rückführung der Altteile, den so genannten ‚Cores‘, da diese das Kernprodukt für die Kreislaufwirtschaft und das Remanufacturing sind. Die Unternehmen nutzen zum Einsammeln der Cores entweder die bestehende Logistik des Teilehandels oder bieten eine eigene Altteilrückführung über Lieferdienste an. In der Regel fallen für den Rücktransport der Gebrauchtteile keine Kosten an. Als Anreiz, das Altteil zurück in den Kreislauf zu geben, dient üblicherweise ein Pfandsystem. Daneben gibt es auch noch das Austausch- sowie das Rückkaufverfahren.
Sind die Cores beim Aufbereiter eingetroffen, werden die Komponenten vor der Demontage bei einer umfangreichen Eingangskontrolle von speziell geschulten Mitarbeitern gesichtet, um zu klären, welche Beschädigungen sicherheitsrelevant und welche nur kosmetischer Natur sind. Was sich nicht mehr aufarbeiten lässt, kommt zum Materialrecycling. Ein typisches K.O.-Kriterium dabei ist, wenn eine Komponente zu alt ist oder schon einmal remanufactured wurde. Anschließend folgt das manuelle Zerlegen der Bauteile. Aufgrund der extrem unterschiedlichen Erhaltungszustände lässt sich dieser Schritt kaum automatisieren.
Welche Kriterien müssen OE-Reman-geeignete Altteile erfüllen?
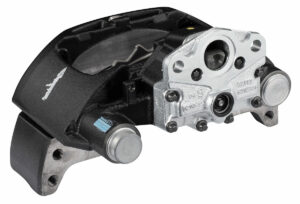
Für die Altteile (Cores) gibt es bei den OE-Herstellern beziehungsweise bei den Aufbereitern strenge Annahmekriterien. Die Qualität der Altteile ist in entsprechenden Dokumenten klar und deutlich in Text- und Bildform beschrieben, wobei die Merkmale für jeden Altteiletyp unterschiedlich sind. Zu den Kriterien gehören unter anderem:
- Das Altteil befindet sich in einem einwandfreien Zustand.
- Es darf nicht gerissen, gebrochen oder verformt sein.
- Das Altteil ist nicht durch nicht-operative Ursachen wie Unfallschäden, Feuer, Risse oder Materialverluste beschädigt.
- Das Altteil wurde nicht unsachgemäß repariert oder gewartet.
Um den Schmutz hunderttausender Straßenkilometer von den Einzelteilen restlos zu entfernen, sind je nach Komponente eine ganze Reihe spezieller Verfahren notwendig: Spritz-Waschanlagen, Pyrolyseanlagen (zum Herunterbrennen von Dichtmittel, Öl, Fett und Lack bei etwa 400°C), Strahlanlagen mit unterschiedlichen Medien sowie Ultraschallbäder. Alle Verfahren sorgen dafür, dass die gebrauchten Einzelteile in neuem Glanz erstrahlen.
Die so gereinigten Teile werden anschließend vermessen, wobei die Toleranzen im Tausendstel-Millimeter-Bereich liegen können. Unterschreitet ein Bauteil die Vorgabe, wird es aussortiert. Manche Einzelteile werden vor der Wiedermontage maschinell aufgearbeitet. So werden beispielsweise die Zylinderlaufbahnen von Kompressoren neu auf Maß gebracht und gehont, um den Ölauswurf auch während des zweiten Lebens möglichst gering zu halten. Defekte Elektronikkomponenten werden getauscht und neu verlötet, gegebenenfalls wird die aktuellste Software-Version aufgespielt. Schließlich geht es ans Wiedermontieren und Testen. Bei OE-Herstellern erfolgt dies nach denselben Maßgaben wie bei der Produktion neuer Originalteile, zum Teil sogar auf denselben Montagelinien. „Für die Wiedermontage gelten die gleichen Qualitätsstandards sowie Prüf- und Messschritte wie bei Originalteilen“, betont ein Sprecher von Knorr-Bremse.
Was bedeutet „wiederaufbereitetes Ersatzteil“?
Eine Definition, die von verschiedenen Organisationen wie APRA, CLEPA, VDA, u. a. unterstützt wird, stellt an das wiederaufgearbeitete Produkt folgende Anforderungen:
- Nach der fachgerechten Wiederaufarbeitung stellt das Remanufacturing-Produkt zumindest eine zum Neuteil äquivalente Funktion sicher.
- Das wiederaufgearbeitete Altteil (Core) wird unter Einsatz industrieller Prozesse gemäß genauen technischen Spezifikationen wiederhergestellt.
- Für ein industriell aufgearbeitetes Teil gilt die gleiche Gewährleistungsfrist wie für ein Neuprodukt.
- Es wird unter Angabe des Herstellers deutlich als wiederaufgearbeitetes Teil gekennzeichnet.
Quelle: Knorr-Bremse
Den Beitrag finden Sie auch in der Print-Ausgabe 4-2024 der Krafthand-Truck.