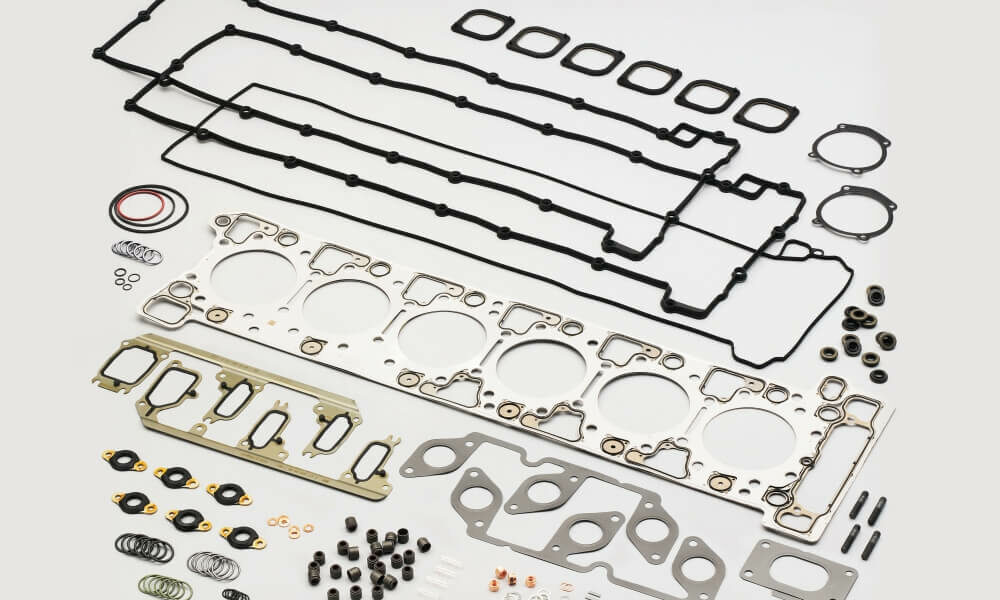
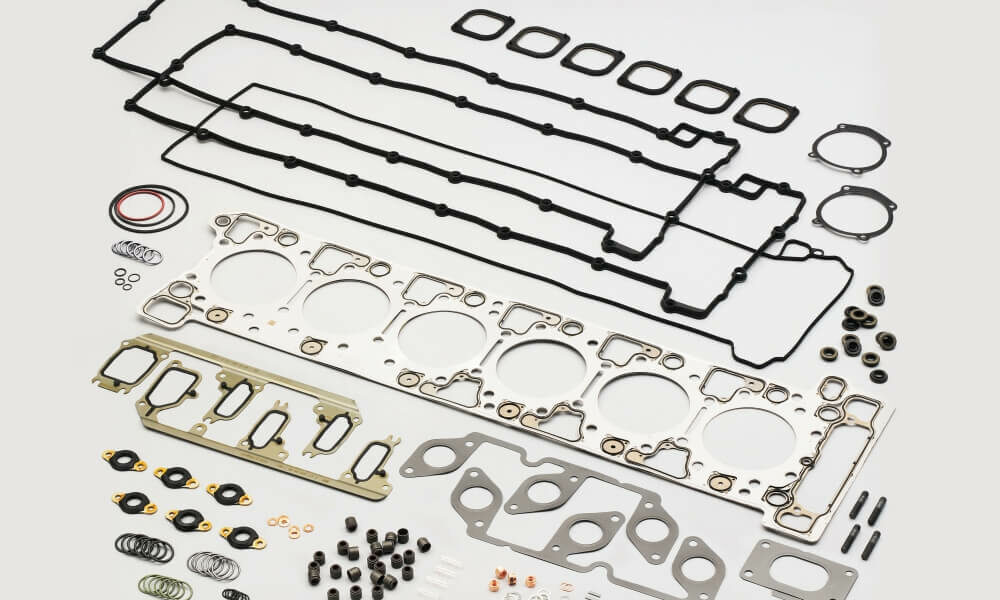
Moderne Dichttechnik
Immer strengere Abgasnormen haben Nutzfahrzeugmotoren zu High-Tech-Triebwerken mutieren lassen. Kaum ein Subsystem blieb dabei unangetastet. Das gilt auch für so scheinbar profane Dinge wie die Dichtungen am Motor: aktuelle Zylinderkopfdichtungen oder Nebendichtungssysteme für Ölwannen, Zylinderkopfhauben oder Abgasanlagen haben kaum noch etwas mit ihren Urahnen gemein. Sie erfordern deshalb auch beim Werkstattfachmann ein Umdenken bei Motorreparaturen. Warum, verraten die Dichttechnikexperten von Elring.
Der im September 2015 losgetretene ‚Diesel-Skandal‘ hat den Selbstzünder schwer in Verruf gebracht: Seither geistern Schlagworte wie ‚Schummel-Software‘, ‚illegale Abschalteinrichtung‘, ‚bewusste Manipulation‘ und ‚Diesel-Gate‘ durch die Medien und werfen ein schlechtes Licht auf das einst so hochgelobte, von Rudolf Diesel erfundene Verbrennungsverfahren.
Dabei lässt der Abgasskandal nahezu vollständig die Errungenschaften der Motorenentwickler vergessen, die den anfänglich als ‚lahm, stinkend und rußend‘ geltenden Motor haben sauber werden lassen. Denn mit jeder neuen, nochmals schärferen Abgasnorm haben Moderne Dichtkunst die Ingenieure erneut beachtliche Klimmzüge machen müssen, um die gesetzlichen Grenzwerte zu unterbieten.
Neue Normen, neue Systeme
Insbesondere zur ab Oktober 2008 für alle neu typgenehmigten Fahrzeuge und ab Oktober 2009 für alle Neuzulassungen geltenden Euro-V-Norm mussten sich die Nutzfahrzeughersteller einiges einfallen lassen und ihre Motoren mit allerlei neuen – und teuren – Technologien versehen oder gar komplett neue Motorenkonzepte entwickeln, um die Grenzwerte einhalten zu können. Mit der Euro V fiel quasi der Startschuss für neue Technologien wie Kraftstoff-Hochdruck-Einspritzsysteme (Common-Rail (CR), Pumpe-Düse (PD), Pumpe-Leitung-Düse (PLD), et cetera), Abgasrückführung und -kühlung, Turboaufladung und auch die Abgasnachbehandlung mit Hilfe einer wässrigen Harnstoff-Lösung, die in den Abgasstrom eingedüst wird (Selektive katalytische Reduktion (SCR)), zog in die Motorentechnik ein. Und um schließlich die derzeit (noch) gültige Euro-VI-Norm (neue Typen ab Dezember 2012, alle Neuzulassungen ab Dezember 2013) erfüllen zu können, mussten die Entwickler die bis dahin vorhandenen Technologien nochmals ‚nachschärfen‘ und um komplexe Abgasreinigungssysteme mit Oxidationskatalysator und Rußpartikelfilter ergänzen.
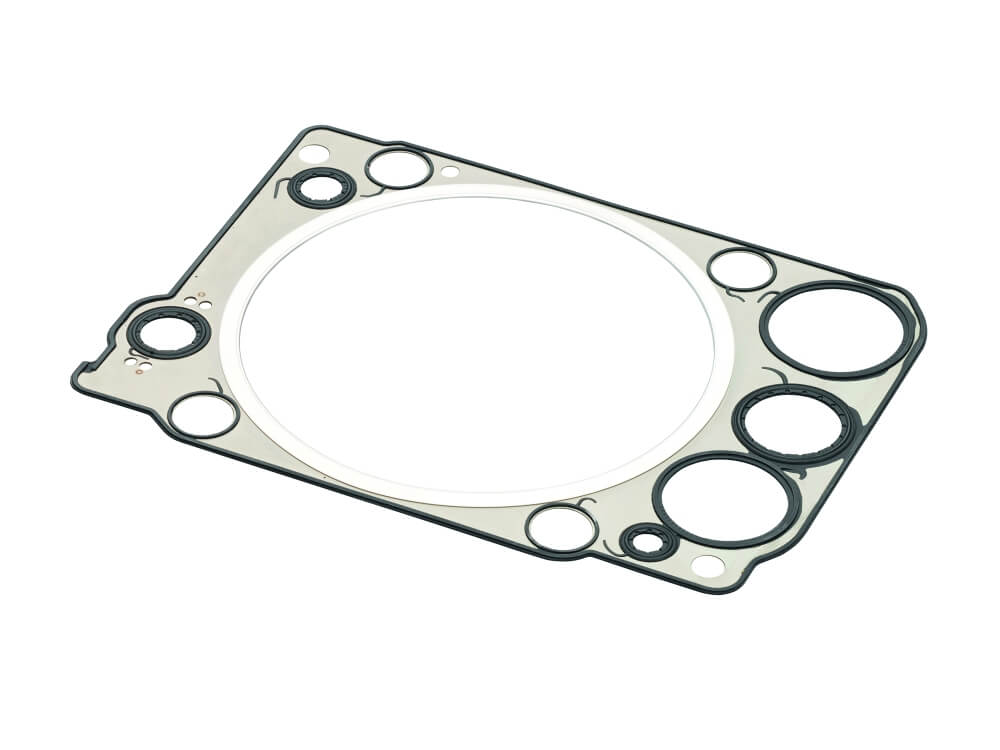
Die Metall-Elastomer-Dichtung eines Einzel-Zylinderkopfs (oben) und eines Sechszylinder-Reihenmotors. Vor dem Einbau einer neuen Dichtung sind in jedem Fall… Bild: Elring
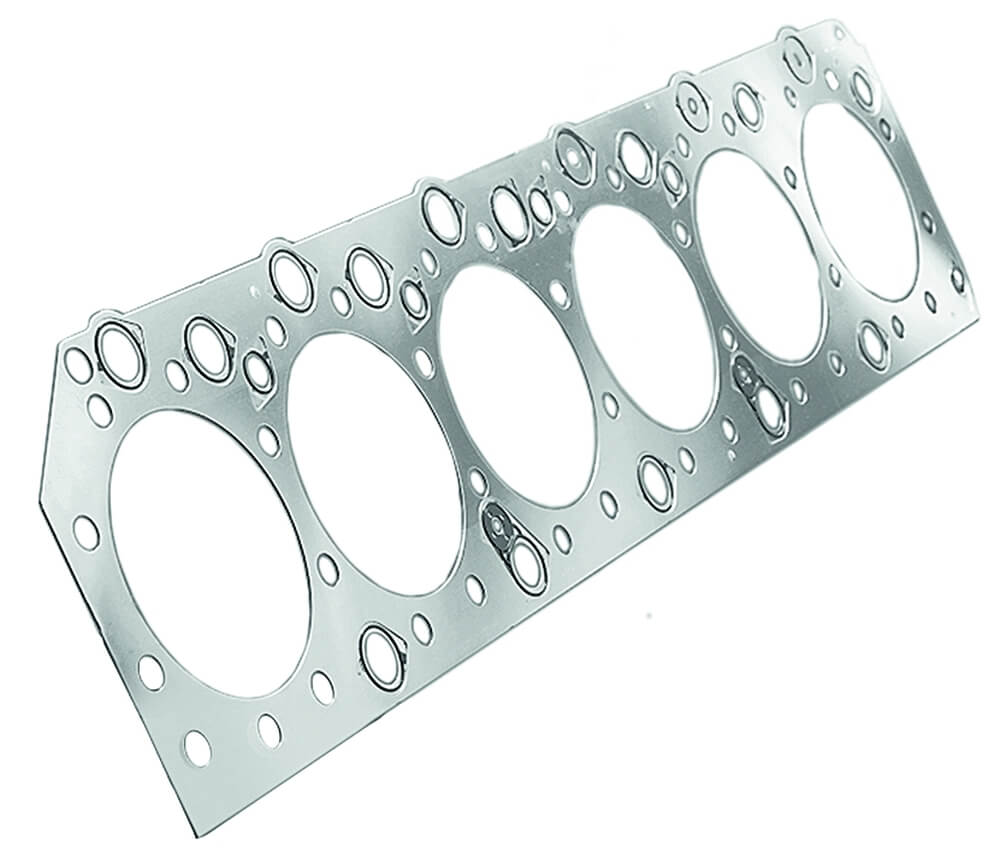
…die Bauteiloberflächen zu prüfen. Eingrabungen muss gegebenenfalls ein Motorenfachmann beseitigen. Bild: Elring
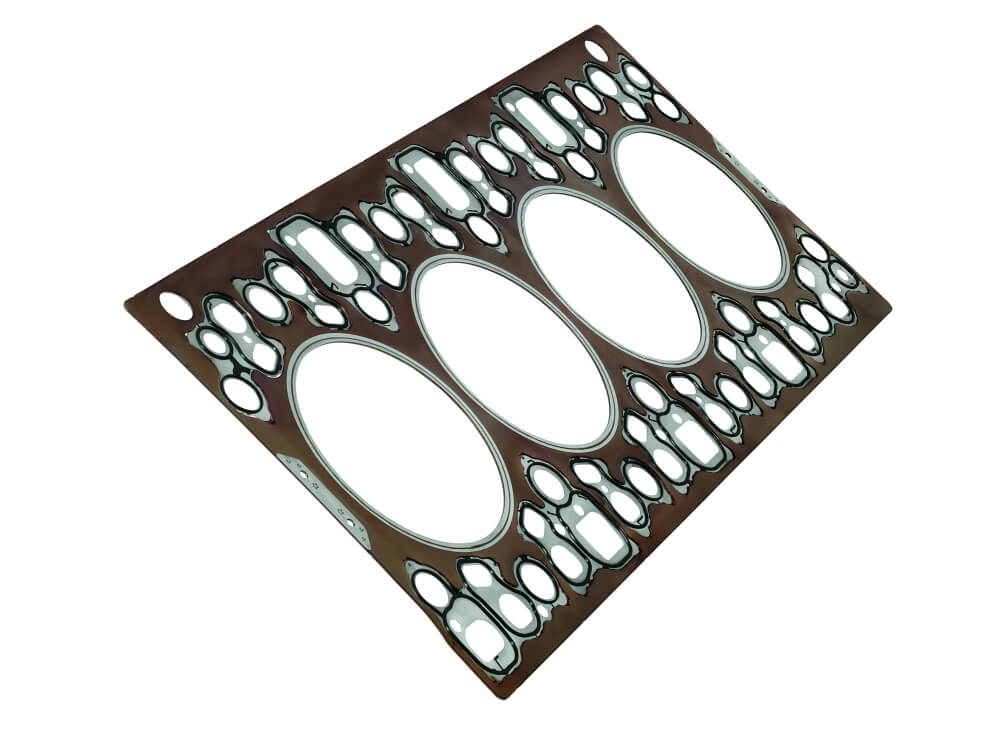
‚Metaloflex‘-Metalllagen-Zylinderkopfdichtungen gehören zu den Schlüsselkomponenten moderner Nutzfahrzeugmotoren. Als Kraftübertragungsglied zwischen Kurbelgehäuse und Zylinderkopf haben sie einen erheblichen Einfluss auf die Kraftverteilung innerhalb des gesamten Verspannungssystems und die dadurch verursachten Bauteileverformungen. Bild: Elring
Neue Motorenkonzepte, neue Anforderungen
Jedes einst noch so moderne Motorenkonzept kommt irgendwann einmal in die Jahre und muss – nicht zuletzt wegen der Abgasgesetzgebung – neu überdacht, überarbeitet oder gar ersetzt werden. „Waren vor wenigen Jahren bei schweren Lkw noch VMotoren mit Stößelstangen und Einzelzylinderköpfen technisch ‚das Maß der Dinge‘, so setzen die Nutzfahrzeugbauer heutzutage wieder auf schwere Reihenmotoren, meist Sechszylinder mit einem einzelnen, großen, einteiligen Zylinderkopf, in dem eine oder zwei obenliegende Nockenwellen rotieren. Aufladesysteme mit einem oder mehreren Turboladern steigern zudem den Gesamtwirkungsgrad des Motors und fördern zudem eine partikelarme Verbrennung“, berichten die Motorenspezialisten des Dichttechnikherstellers Elring. „Das alles hat natürlich auch einen großen Einfluss auf die Dichtungs technologie, insbesondere der Zylinderkopfdichtung“, konstatieren die im schwäbischen Dettingen an der Erms beheimateten Dichttechnikfachleute.
Demnach gibt es zahlreiche Parameter und Einflussgrößen, die sich gravierend auf die Dichtungen in solchen Aggregaten auswirken. Leichtbau beispielsweise. Denn manche Hersteller fertigen den Zylinderkopf ihrer schweren Dieselmotoren aus speziellen Aluminiumlegierungen. Dies, sowie das veränderte Gesamtdesign, also die Rückkehr zum Reihenmotor mit einteiligem Zylinderkopf, beeinflusst den Experten zufolge sowohl die Bauteilsteifigkeit als auch die Bauteilbewegungen extrem. Hinzu komme, dass die Druckspitzen, etwa der Kraftstoffeinspritzung und des Verbrennungsenddrucks, stark gestiegen sind. „Die hohen Enddrücke erfordern nicht nur standhafte Motorenbauteile, auch die Dichttechnik muss hier Schritt halten“, konstatieren die Fachleute. Darüber hinaus müssten bei der Auslegung von Zylinderkopfdichtungen (ZKD) die vermehrten Dichtspaltschwingungen sowie die deutlich höheren Verbrennungstemperaturen beachtet werden.
Hochkomplexe Dichttechnologien
Zylinderkopfdichtungen für aktuelle EuroVIMotoren sind den Fachleuten von Elring zufolge „Wunderwerke der Technik“. Meist als MetallElastomer (ME)Variante und als einteilige Reihendichtung gefertigt, vereinen sie demnach alle derzeit bekannten Technologien: Der Dichtungskörper selbst kann aus einoder mehrlagigen Trägerlagen aufgebaut sein. Massive, aber dennoch flexible Brennraumsicken stellen dabei die Dichtfunk tion bei allen Betriebszuständen sicher. Um flüssige Medien (Motoröl, Kühlmittel) selbst bei hohen Dichtspaltschwingungen mit Variablen bei den Klemmkräften im Hinterland sicher abzudichten, werden elastomere Elemente entweder an den Dichtungskörper angespritzt oder als Insert mittels Lasertechnologie eingeschweißt.
Bei großen Motoren, die konstruktionsbedingt nach einer exakten Kontrolle der Schraubenkräfte im Verbund verlangen, werden die Klemmkräfte mittels eines höhenprofilierten Stoppers exakt gesteuert eingeleitet. „Hier ist Entwicklungs-Know-how gefragt, über das nur Entwicklungspartner der Motorenindustrie verfügen“, konstatieren die Dettinger Dichttechnikexperten. Die bei Pkw-Diesel motoren weit verbreitete mehrlagige MetallSickendichtung indes ist bei den großen Nutzfahrzeugmotoren bis auf wenige Ausnahmen kaum zu finden.
Auch Nebendichtungen, etwa für Zylinderkopfhauben oder Ölwannen sowie Flanschoder Pumpendichtungen, mussten an die verschärften Bedingungen angepasst werden. Deshalb sind bei aktuellen Euro-VI-Motoren kaum noch Gummi-Kork-Dichtungen, Papier oder flächenverpresste Verbundstoffvarianten zu finden, diese wurden fast ausnahmslos durch Elastomer-Dichtungen, entweder formverpresst oder mit Dichtlippen versehen, oder durch linienverpresste, einlagige Metalldichtungen ersetzt, die Elring unter dem Markennamen ‚Metaloseal‘ herstellt.
Know-how essenziell für die fachgerechte Reparatur
Mit dem technischen Fortschritt bei der Dichttechnologie ändern sich zwangsläufig auch die Anforderungen an das Knowhow des Werkstattfachmanns. Denn was früher richtig und üblich war, kann bei modernen Dichtungen zu Problemen führen. So mussten beispielsweise früher Radialwellendichtringe aus Fluorkautschuk (FKM) vor dem Einbau geschmiert beziehungsweise gefettet werden, um eine lange Lebensdauer zu erreichen. Für moderne Radialwellendichtringe aus Polytetrafluorethylen (PTFE, Handelsname‚ Teflon‘) wäre dieses Vorgehen ‚tödlich‘ und würde zu einer baldigen Leckage führen: Sie müssen absolut trocken eingesetzt werden. Und anschließend ist vor dem Motorstart eine Wartezeit von bis zu vier Stunden einzuhalten. Doch das ist laut Mario Rauch, technischer Trainer bei Elring, nur ein Beispiel von vielen.
Damit Nutzfahrzeug-Profis mit dem technischen Fortschritt mithalten können und technisch stets ‚Uptodate‘ sind, hat Elring ein breit angelegtes Weiterbildungsangebot aufgelegt. Zu finden ist dieses auf der ElringWebsite www.elring.de. „Hier bieten wir eine Anwender-Hotline, Mailkontakt zu unseren Spezialisten und viel Wissenswertes, etwa ServiceInformationen (TSI) und MontageVideos, die den Einbau und die Anwendung von Spezialwerkzeugen zeigen“, berichtet Rauch. Darüber hinaus gibt es mit der ‚ElringAkademie‘ eine OnlinePlattform, auf der KfzProfis ihr Knowhow prüfen und im Selbststudium erweitern können. Elring hat hierfür das sogenannte ‚Virtuelle Klassenzimmer‘ ins Leben gerufen. Wer dort sein ‚Dichttechnik-Examen‘ abschließen und den Titel ‚Certified ElringExpert 2019‘ erwerben möchte, kann dies unter http://akademie.elring.de/ tun.
Den Beitrag finden Sie auch in der Print-Ausgabe 2/19 der Krafthand-Truck.