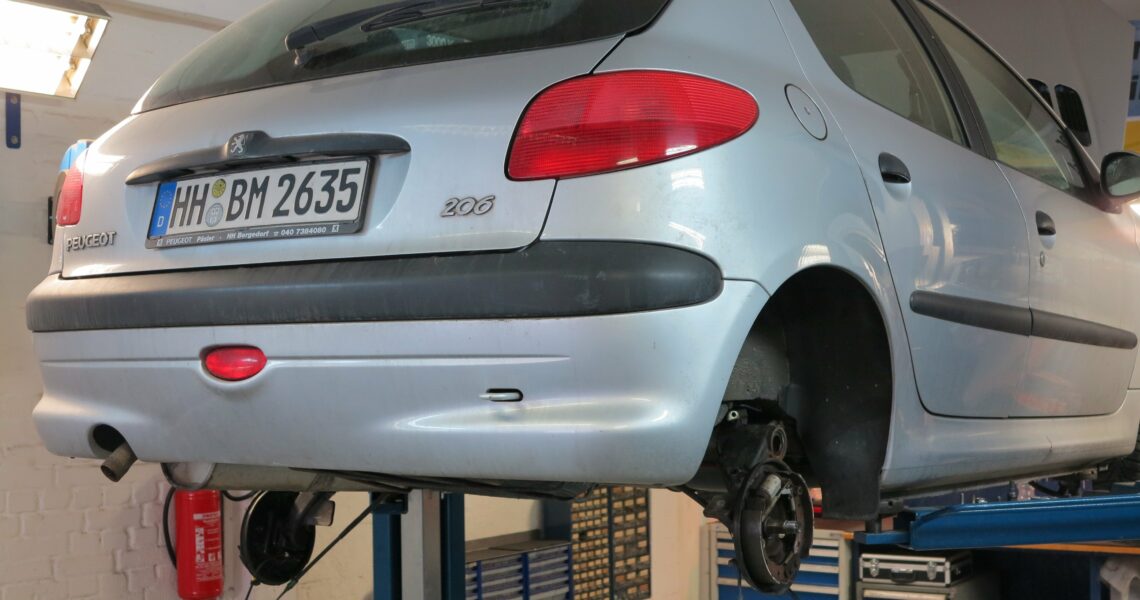
Zeitwertgerechte Instandsetzung älterer PSA-Modelle
Bei rund 14,5 Mio. Modellen der PSA-Gruppe ist herstellerseitig bis dato keine Hinterachsreparatur bei eingelaufenen Achszapfen vorgesehen. Dies bedeutet für einen großen Teil der Fahrzeuge das vorzeitige Aus, denn ein Tausch der Hinterachse ist schlichtweg zu teuer und somit unwirtschaftlich. Ruville bietet jetzt eine Reparaturlösung für die betroffenen Fahrzeuge an. KRAFTHAND begleitete eine Hinterachs-Instandsetzung in der Praxis.
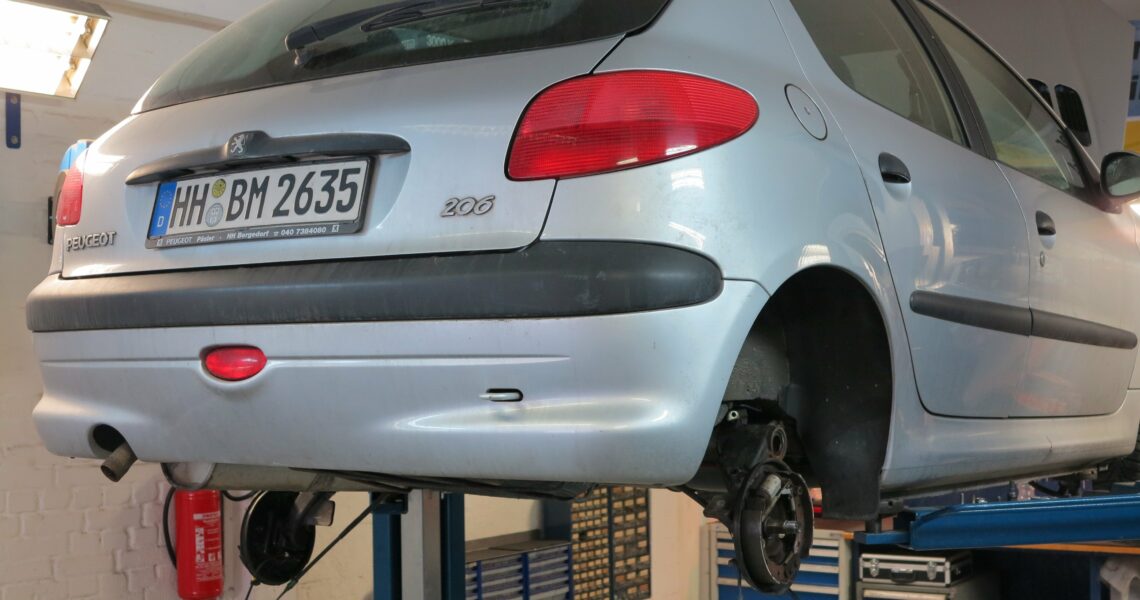
Bei den Marken Citroën und Peugeot des französischen Automobilkonzerns unterliegt der Zapfen der Hinterachse einem sehr hohen Verschleiß. Das macht sich für den Fahrer in der Regel mit unangenehmen Geräuschen während der Fahrt bemerkbar und ist in der Folge aufgrund einer Schiefstellung der Hinterräder für den Kfz-Profi auch mess- und sichtbar. Durch diese Schrägstellung der Räder verschlechtert sich das Fahrverhalten und andere Fahrwerkskomponenten werden in Mitleidenschaft gezogen. Außerdem stellt dies einen erheblichen Mangel bei der Hauptuntersuchung dar, wodurch die Zuteilung der Prüfplakette entfällt.
Die hohen Laufleistungen sowie der geringe Arbeitsbereich der Wälzlager führen laut Anbieter zu einem mechanischen Einlaufen der Wälzlager in den Achszapfen. Zudem führen Durchlässigkeiten poröser Dichtringe zu erheblicher Korrosion am Achszapfen, was Zapfen und Lager innerhalb kürzester Zeit zerstört. Vereinzelt traten bereits Fälle auf, in denen durch die extreme Radschiefstellung Radinnenläufe an- beziehungsweise durchgeschliffen wurden.
Um betroffene Fahrzeuge – oftmals schon mit geringen Laufleistungen – wieder instand zu setzen, gab es als Lösung nur den Tausch des kompletten Achskörpers. Die einzelnen Achszapfen konnte die Werkstatt nicht separat wechseln. Vom Fahrzeughersteller ist laut Reparaturunterlagen nur eine kostenintensive, komplette Erneuerung der Hinterachse vorgesehen. Allerdings sind in diesem Fall die Reparaturkosten meist so hoch, dass sie den Zeitwert der Fahrzeuge bei Weitem übersteigen. Eine Reparatur kommt dann einem wirtschaftlichen Totalschaden gleich. Viele Fahrzeuge werden deshalb ersetzt, beispielsweise durch ein Neufahrzeug, und gehen somit den Werkstätten als Kunden verloren.
Die Lösung
Der Systemspezialist Ruville bietet seit Kurzem für eine zeitwertgerechte Reparatur der Hinterachse ein maßgeschneidertes Reparaturkit in Kombination mit einem speziell dafür entwickelten Werkzeugsatz an. Bei den Modellen Peugeot 106, 206, 306, 309 und Partner sowie Citroën Saxo, AX, Berlingo, Xsara und ZX kann die Werkstatt damit jetzt eine entsprechende Reparatur anbieten – den Angaben zufolge zu 40 Prozent geringeren Kosten. Informationen zur genauen Fahrzeugzuordnung sowie Reparatursätze und Werkzeuge stehen in den Ruville-Katalogen oder TecDoc. Mit fünf baureihenbedingt unterschiedlichen Kits sollen rund 98 Prozent der betroffenen Fahrzeuge abgedeckt sein.
Alle Reparaturkits für die Hinterachsen bestehen aus jeweils zwei äußeren und inneren Lagern, zwei Achszapfen und dementsprechenden Dichtringen sowie allen zur Reparatur notwendigen Kleinteilen, wie Schrauben, Muttern und speziellen Lagerfetten. Der ausschließlich bei Ruville erhältliche Spezialwerkzeugsatz für den Austausch der Achszapfen beinhaltet neben einer kurzen zwei lange Spindeln, ebenso zwei Axiallager, kleine und große Führungsringe, ein Abstützrohr, zwei Druckstücke und alle notwendigen Kleinteile.
Vorarbeiten
Der Kfz-Profi demontiert als erstes auf einer geeigneten Hebebühne die Räder des Fahrzeugs. Anschließend muss er den gesamten Arbeitsbereich an den Aufnahmen der Drehstäbe und besonders die Nut im Übergangsbereich des Achsrohrs aus Blech zum Achsjoch aus Stahlguss sorgfältig reinigen. Des Weiteren sind die Hydraulikleitungen an den Bremssätteln oder bei Trommelbremsen an den Bremszylindern abzuschrauben sowie die elektrischen Steckverbinder zu den Raddrehzahlsensoren zu trennen.
Danach demontiert der Mechatroniker die Bremstrommeln beziehungsweise die Bremssättel und hängt die Handbremsseile aus. Zum Schluss sind noch beide Stoßdämpfer auszubauen sowie der Abstand zwischen Kotflügelkante und Radnabenmitte zu messen. Dieses Maß dient zur späteren Kontrolle der abgeschlossenen Reparatur. Zusätzlich sollte der Mechatroniker auch die Gewindespindeln, Muttern und Axiallager vor jedem Gebrauch sorgfältig reinigen und ausreichend mit dem im Werkzeugsatz beiliegenden Fett schmieren. Verschlissene Spindeln oder Muttern müssen nachgeschnitten oder bei Bedarf erneuert werden. Ruville untersagt übrigens ausdrücklich den Einsatz von Druckluftwerkzeugen.
Ausbau
Nach den Reinigungs- und Vorbereitungsarbeiten entfernt der Kfz-Profi auf der linken Fahrzeugseite einen Plastikstopfen und dreht die Fixierschraube aus der Stabilisatorhalteplatte heraus. Mit einer Schraube wird anschließend über das Gewinde des Stopfens das Stabilisatorhalteblech abgedrückt. Auf der rechten Fahrzeugseite wird analog die Fixierschraube gelöst und der Mechatroniker kann jetzt den Stabilisator nach rechts herausziehen.
Um die Drehstäbe auszubauen, dreht er zunächst die Halteschrauben aus den Drehstäben heraus und entfernt die Exenterscheiben. Die so freigelegten Nuten sind sorgfältig zu reinigen. Anschließend markiert er verwechslungssicher die Position der Drehstäbe in ihren Verzahnungen. Die Drehstäbe treibt er jetzt in Richtung ihrer größeren Verzahnung aus dem Gehäuse heraus. Die Schwingarme kann der Werkstattfachmann nun vom Achszapfen abziehen, gegebenenfalls ist ein Spezialwerkzeug des jeweiligen Fahrzeugmodells zu verwenden. Als letzter Arbeitsschritt vor dem Auspressen ist noch die Einpresstiefe der Zapfen im Achsrohr zu messen und in die Tabelle der beigefügten Einbauanleitung des Reparaturkits einzutragen.
Vor dem Schweißen schiebt der Mechatroniker eine Schutzhülle auf die kurze Werkzeugspindel, schraubt die mitgelieferte M20-Mutter des Reparatursatzes mit Kragen zur Fahrzeugaußenseite auf die Spindel und führt dieses in den Achszapfen ein. Sicherheitshalber ist die Batterie vor dem Schweißen abzuklemmen. Jetzt verringert er durch Auftragen einer MAG-Schweißnaht den Achszapfen-Innendurchmesser auf mindestens 24 mm, so dass die eingeführte Spindel mit Mutter nicht mehr herausgezogen werden kann. Hinweis: Die Mutter ist weiterhin lose im Achszapfen und ist nicht mit dem Achszapfen verschweißt.
Nach dem Schweißen wird die Spindel mit dem Schutzrohr entfernt. Danach reinigt der Mechatroniker das Schutzrohr, denn es eignet sich zum mehrmaligen Gebrauch. Zusätzlich ist am Außendurchmesser ebenfalls eine Schweißnaht aufzubringen. Nach einer kurzen Abkühlphase stülpt der Kfz-Techniker das Druckrohr, Endstück, Axiallager und Mutter aus dem Werkzeugsatz über den Zapfen und verschraubt mit der Werkzeugspindel mit mindestens zehn Umdrehungen die zuvor im Achszapfen eingelegte Mutter. Der Achszapfen wird nun über die Werkzeugmutter mit geeignetem Werkzeug herausgezogen. Bei den Modellreihen AX, Saxo und 106 ist auf dem Achszapfen zusätzlich ein Laufring als Dichtfläche vorhanden. Diesen Ring muss der Mechatroniker vorsichtig abnehmen und aufbewahren. Diese Arbeitschritte sind auf beiden Fahrzeugseiten auszuführen.
Einbau
Vor dem Einbau der neuen Achszapfen sollte der Mechatroniker die Achsrohrinnenflächen auf Verschleiß und Verwendbarkeit prüfen. Wird an dem Achsrohr nichts beanstandet, ist dieses zu reinigen und sparsam einzufetten. Anschließend kann die Montagepaste aus dem Reparaturkit dünn und gleichmäßig auf den einzupressenden Bereich an der breiten Anfassung des neuen Zapfens und den Achsrohreingang umfänglich aufgetragen werden. Der Kfz-Profi zieht jetzt den neuen Achszapfen mit Hilfe der langen Spindeln, Druckstücke und Axiallager sowie Werkzeugsatzmuttern auf die zuvor ermittelte Einbautiefe ein.
Als zusätzliche Hilfe haben die neuen Achszapfen eine umlaufende Nut, als ‚Hilfsmaß’ dafür, wie weit der Zapfen im Achsrohr sitzen muss. Beim Einziehen sollte der Mechatroniker ständig kontrollieren, dass der Zapfen auf beiden Seiten parallel zum Achsrohr eingezogen wird. Leichte Schläge mit einem Gummihammer auf das mittlere Achsrohr erleichtern das Einziehen. Ein Schlagschrauber hingegen könnte in diesem Fall, weil kein deutlicher Druckpunkt spürbar ist, das Achsrohr beschädigen.
Im nächsten Arbeitsschritt erneuert der Mechatroniker nach Herstellervorgaben die Lagerung und Dichtringe der Schwingarme. Anschließend ist der Achszapfen zu fetten und die Schwingarme sind mit neuer und ebenfalls gefetteter Lagerung wieder aufzusetzen. Danach werden die Drehstäbe wieder montiert und auf die Markierungen positioniert sowie die zuvor gemessenen Maße wieder eingestellt. Jetzt kann der Kfz-Profi die Exenterscheiben der Drehstäbe in die gereinigten Nuten legen und mit den Halteschrauben befestigen.
Der Stabilisator lässt sich nun montieren. Der Mechatroniker sollte das zuvor ermittelte Kontrollmaß überprüfen und bei Abweichungen die Positionierung der Drehstäbe korrigieren. Zum Schluss montiert und befestigt er die anderen Komponenten in umgekehrter Reihenfolge und entlüftet die Bremsanlage. Eine Probefahrt sollte die erfolgreiche Reparatur abschließen.
Schreiben Sie den ersten Kommentar