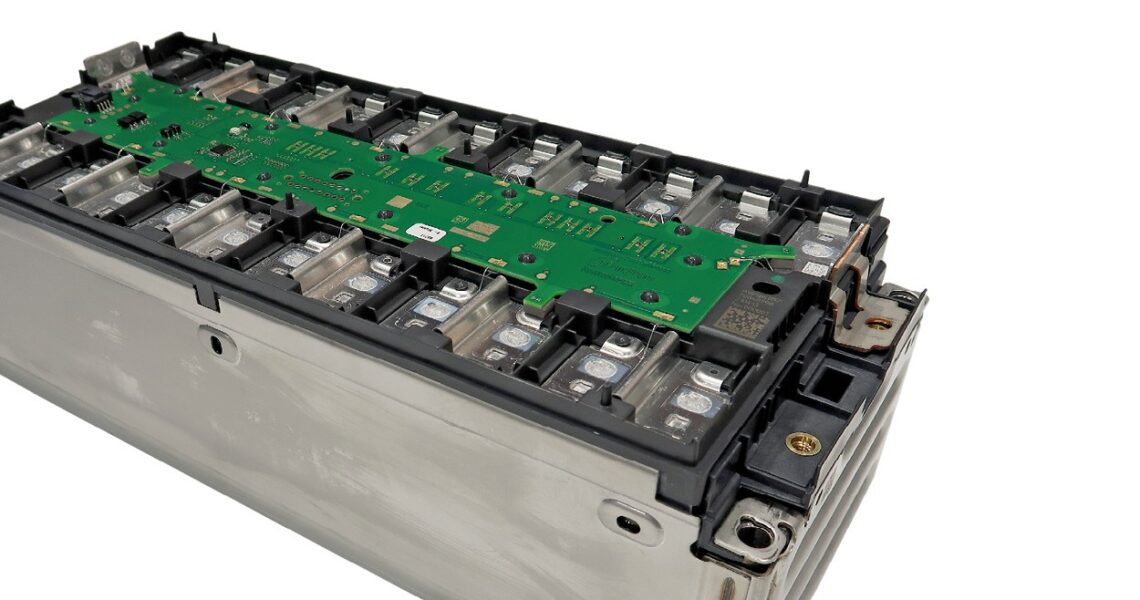
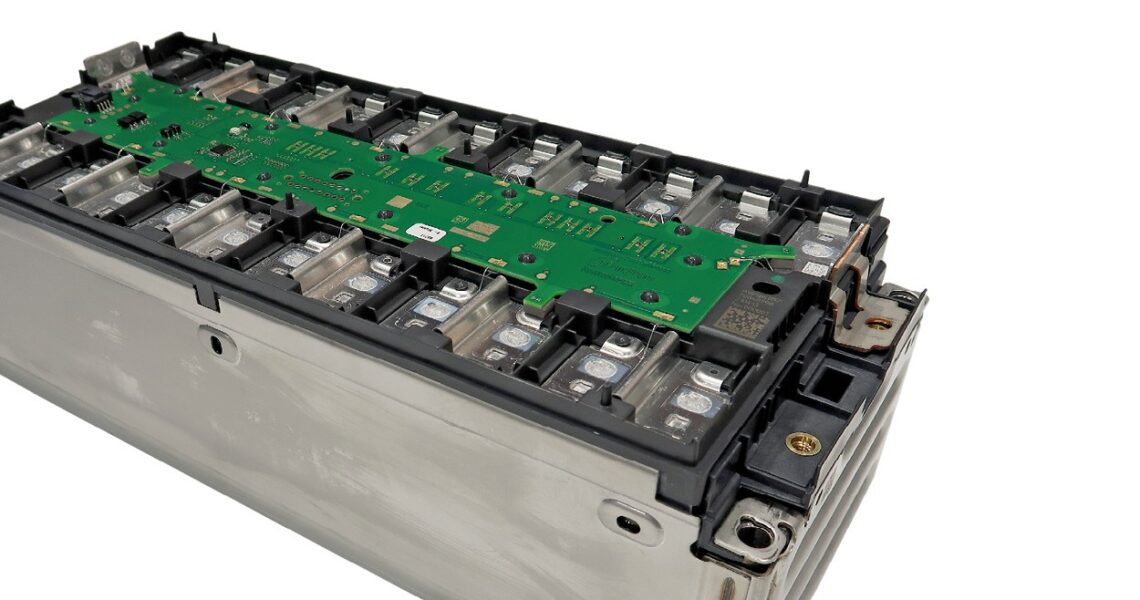
Fahrzeughersteller machen sich nicht zuletzt aufgrund der Nachhaltigkeitsdebatte von E-Fahrzeugen Gedanken über den Umgang mit schwächelnden Traktionsbatterien von in die Jahre gekommenen E-Autos. So wurde beispielsweise die Software BattMAN (Battery Monitoring Analysis Necessity) von Audi für die schnelle und genaue Analyse der Hochvoltbatterie des Audi e-tron entwickelt.
Laut Unternehmen prüft das Gerät dabei zuerst, ob die Batterie überhaupt kommunikationsfähig ist und Daten übermittelt. Danach können Fehlermeldungen, Isolationswiderstand, Kapazität, Temperaturen und Zellspannungen festgestellt und angezeigt werden. Daraus ergibt sich der Gesamtzustand der Batterie.
Wichtig zu wissen: Beim überwiegenden Teil der Autobauer gilt eine Batterie erst bei einer Kapazität unter 70 Prozent als verschlissen – zumindest, wenn es um die Garantie oder Gewährleistungsansprüche geht. Wie dem auch sei: Je nach Leistungsfähigkeit entscheidet der Automobilhersteller nach dem Prüfvorgang, ob die HV-Batterie ganz oder in Teilen wieder in einem Fahrzeug eingesetzt wird, ein zweites Leben als mobiler oder stationärer Energiespeicher bekommt oder das Material durch einen speziellen Recyclingprozess zurück in die Zellproduktion geführt wird. Es kommen demnach drei Möglichkeiten infrage:
Remanufacturing bedeutet, dass die Batterie aufgrund ihres guten bis sehr guten Leistungszustands wiederaufbereitet und danach im Rahmen einer zeitwertgerechten Reparatur als Austauschteil weiterhin in einem E-Fahrzeug eingesetzt wird. Entsprechende Konzepte sind derzeit in Prüfung und Erarbeitung.
Second Life bedeutet, dass die Batterie einen mittleren bis guten Leistungszustand hat und noch jahrelang in einem „zweiten Leben“ woanders genutzt werden kann. Zum Beispiel in einer flexiblen Schnellladesäule, einem mobilen Laderoboter, einem fahrerlosen Transportsystem, einem Flurförderfahrzeug, einem Heimspeicher oder einem Notstrom-Sicherungs-System.
Effizientes Recycling erfolgt in der Pilotanlage von Volkswagen Group Components in Salzgitter, wo nur die wirklich ausgedienten Akkus durch mechanische Verfahren schonend in einzelne Fraktionen wie Aluminium, Kupfer, Kunststoffe und „schwarzes Pulver“ zerlegt werden. Letzteres enthält die wertvollen Batterierohstoffe Lithium, Nickel, Mangan und Kobalt sowie Graphit, die durch spezialisierte Partner mit hydrometallurgischen Verfahren sortenrein getrennt und danach erneut zu Kathodenmaterial verarbeitet werden können.