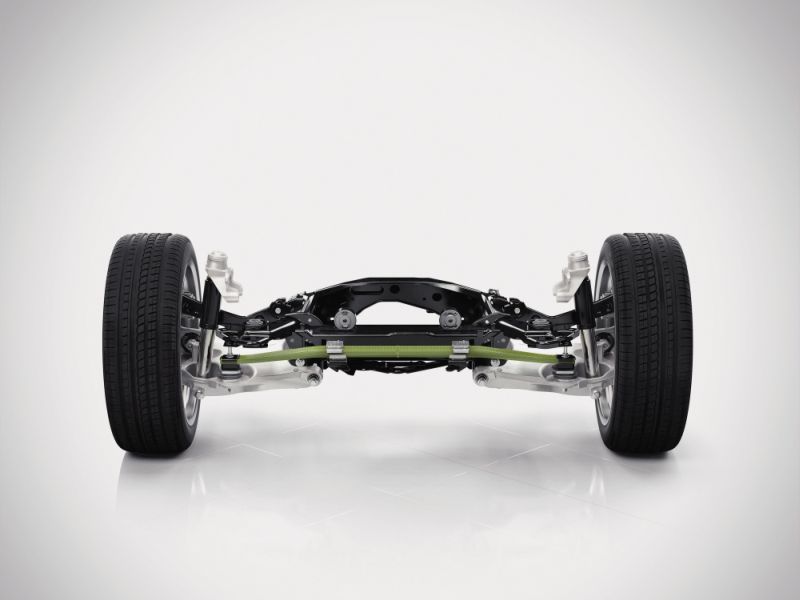
Damit die Autobauer die gesetzlichen Vorschriften zur Reduzierung der CO2-Emissionen erfüllen können, sind sie bestrebt, jedes unnötige Gramm Gewicht zu vermeiden. Um das über entsprechende Leichtbaukonzepte voranzutreiben, wird der Einsatz von Verbundwerkstoffen immer wichtiger.
Im Vergleich zu Metallbauteilen bringen sie in Sachen Gewicht Vorteile mit sich. In diesem Kontext nimmt auch die Bedeutung von Matrixharzen und Klebstoffen zu. Schließlich sind diese zur Fertigung und Montage von Verbundwerkstoffteilen, einschließlich hybrider Kunststoff/Metallkonzepte notwendig.
Ein aktuelles Beispiel wie Harze zur Gewichtsreduzierung beitragen, ist die glasfaserverstärkte Blattfeder, die Volvo im aktuellen XC90 sowie im S90 und im V90 einsetzt. Für die Fertigung der von Benteler-SGL entwickelten Feder kommt Loctite MAX 2 zum Einsatz, ein von Henkel entwickeltes Zweikomponenten-Matrixharzsystem für Polyurethanverbundwerkstoffe. Die innovative Blattfeder bringt eine Gewichtsreduzierung von 4,5 kg mit sich.
Weitere Anwendungen
Weiterhin nimmt die Bedeutung von innovativen Klebern und Harzen im Bereich der Karosserie zu. Denn die Automobilhersteller wollen zunehmend Stahl durch faserverstärkte Kunststoffe ersetzen, was einen wachsenden Bedarf an effizienten Lösungen zum Verkleben hybrider Materialkombinationen mit sich bringt. Die dafür notwendigen Kleber müssen auf die unterschiedlichen Wärmeausdehnungskoeffizienten ausgelegt sein, ebenso wie sie hohe Ansprüche an Festigkeit bei gleichzeitiger Elastizität erfüllen müssen.
Henkel bietet den Automobilherstellern mit dem Klebstoff Loctite UK 2015 ein Produkt, das auf 2K-Polyurethantechnologie basiert und für das Verkleben von tragenden Karosseriebauteilen geeignet ist. Ob diese aus faserverstärkten Kunststoffen oder elektrolytisch beschichtetem Stahl oder Aluminium besteht, spielt keine Rolle.