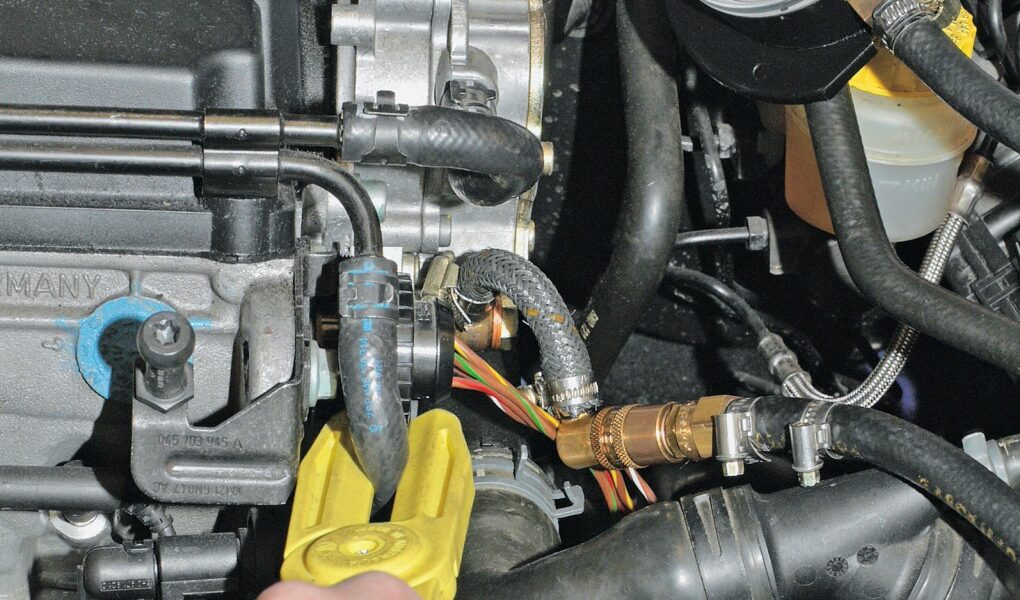
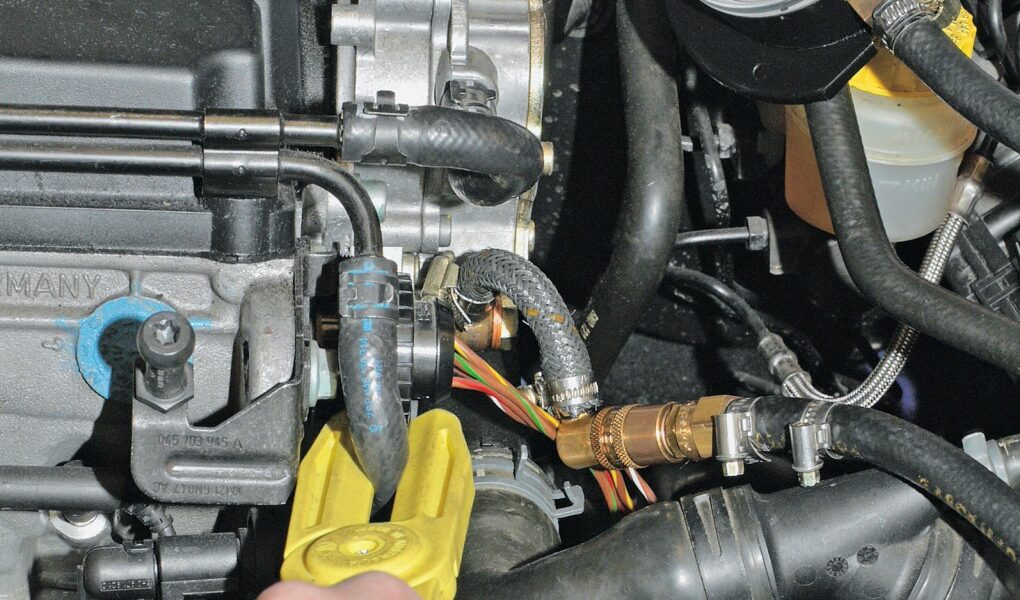
Auch wenn Pumpe-Düse-Einspritzsysteme je nach Marke seit etwa zehn Jahren nicht mehr in Serie verbaut werden, rollen immer noch Millionen Dieselautos mit dieser Technik über Deutschlands Straßen. Entsprechend müssen sich Kfz-Profis noch geraume Zeit damit auseinandersetzen.
Der Hauptgund, warum die Ära der Pumpe-Düse-Einspritzung (PDE), welche erstmals 1998 in einem Pkw serienmäßig verbaut wurde, vor etwa einem Jahrzehnt zu Ende ging, ist in der seit 2009 geltenden Abgasnorm Euro 5 und weiterführender Emissionsvorschriften zu suchen.
Denn während die Ingenieure bei der heute fast ausnahmslos zum Einsatz kommenden Common-Rail-Anlage große Freiheiten bei der Gestaltung des Einspritzkennfelds haben und somit die Rohemissionen besser im Zaum halten können, sind diese Möglichkeiten bei der PDE deutlich eingeschränkt.
Der Grund dafür liegt in der PD-systembedingten nockengetriebenen Druckerzeugung. Wie jeder Kfz-Profi weiß, wird in jedem Pumpenelement der Druck mit dem entsprechenden Nockenhub erzeugt.
Das Problem dabei: Das Anliegen des nötigen Dieseldrucks im PD-Injektor für die Vor- (ca. 180 bar) und Haupteinspritzung (ca. 300 bar) hängt maßgeblich von der Gestaltung der Nockenwelle ab. Damit sind diese Einspritzungen nur in einem bestimmten Zeitfenster zu verwirklichen.
Gleiches gilt natürlich für die zur Schadstoffreduzierung nötigen Nacheinspritzungen, welche je nach Motortyp und Betriebszustand bis zu zweimal pro Arbeitstakt erfolgen. Um diese allerdings überhaupt realisieren zu können, bedarf es unter anderem einer aufwendigen und somit relativ teuren Nockengeometrie.
Hinzu kommt: Lange galten Motoren mit einem PD-System gegenüber vergleichbaren Common-Rail-Aggregaten als verbrauchsgünstiger und oft als drehmomentstärker. Vorteile, die zum Ende der PD-Ära aufgrund der optimierten CR-Systeme nicht mehr wirklich vorhanden waren.
Um die fehlerfreie Funktion eines Pumpe-Düse-Systems zu garantieren, müssen diverse Signale und Sensoren funktionieren. Fällt zum Beispiel der Bezugsmarkengeber aus, ist kein Motorbetrieb mehr möglich. Aber wie wirkt es sich aus, wenn der Kraftstofftemperatur- oder andere Sensoren spinnen? mehr …
Denn die hohen Einspritzdrücke der PD-Systeme (Magnetventilsysteme bis 2.050 bar und Piezoventile bis 2.200 bar), die lange Zeit im CR-System nicht erreichbar waren, ließen sich Ende der Nullerjahre je nach Variante auch mit Common-Rail-Anlagen (bis zu 2.000 bar) nahezu erreichen.
Allerdings kommt es für die Fehlersuche auf andere Aspekte und essenzielles Systemverständnis an.
Für das einwandfreie Funktionieren eines Einspritzsystems ist die Kraftstoffversorgung grundlegend. Deshalb und weil Probleme mit dem Förderdruck durchaus zu Fehlerspeichereinträgen führen, welche den Fehler an anderer Stelle vermuten lassen, widmen wir uns zunächst dem Kraftstoffsystem. Was keineswegs dem üblichen Ablauf entgegensteht, die Fehlersuche mit dem Auslesen des Fehlerspeichers und der Systemparameter zu beginnen.
Bevor der Kfz-Profi den Förderdruck über den Prüfanschluss der am Zylinderkopf angeflanschten Kraftstoffpumpe misst, muss er natürlich sicherstellen, dass sich genügend Diesel im Tank befindet. Zudem sollte eine Falschbetankung mit Benzin ausgeschlossen sein.
Das Manometer angeschlossen, muss bei den Zweiventilmotoren ein Systemdruck von mindestens 7,5 bar bei einer vorgegebenen Nenndrehzahl anliegen. 4.000/min sind es beispielsweise für einen 1,9-l-TDI. Bei Vierventilmotoren muss laut Bosch der Förderdruck hingegen 10,5 bar betragen.
Während des Startvorgangs oder im Leerlauf sollten wenigstens 1 beziehungsweise 3 bar anliegen, wie Hubertus Günther im Kapitel „Das Pumpe-Düse-System“ des Krafthand-Buchs „Common-Rail-Systeme in der Werkstattpraxis“ schreibt.