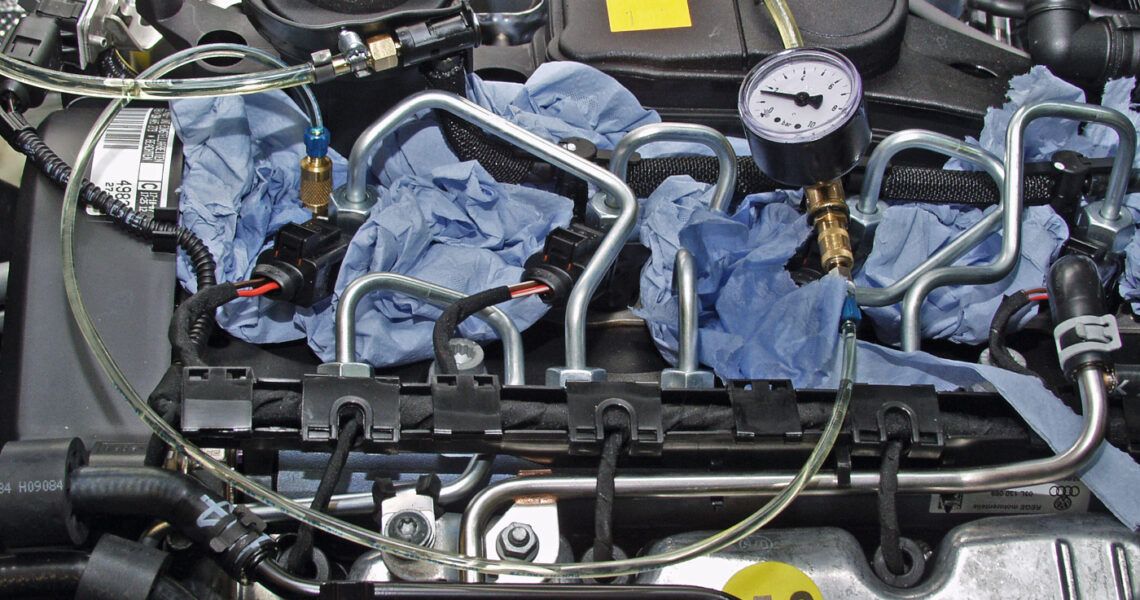
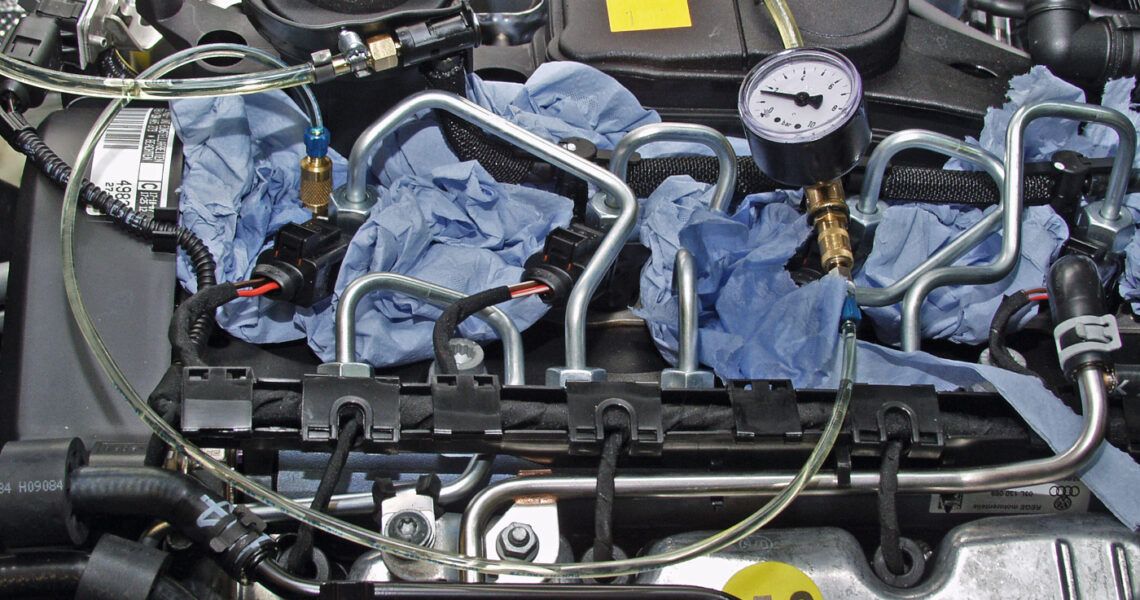
Ein außerhalb der Toleranz liegender Raildruck kann viele Gründe haben – die Ursache lässt sich aber durch Prüfungen meist lokalisieren. Schwierig wird es allerdings, wenn sich gleichzeitig ein neuer Fehler einschleicht – ein Experte schildert einen Fall aus der Praxis.
Ein Kollege aus einer befreundeten Werkstatt bat mich um Rat. Er hatte an einem älteren Transporter schwankenden Raildruck. Da bei diesem Fahrzeug Probleme mit dem Druckregelventil am Rail bekannt sind, hatte er das Druckregelventil erneuert. Bei einer Probefahrt stellte er fest, dass bei warmem Motor und hoher Last das Steuergerät einen Fehler setzte und in den Notlauf ging. Im Fehlerspeicher stand „Regelabweichung Raildruck“.
Ich besorgte mir einen Hydraulikplan der Anlage (Bild weiter unten). Es handelte sich um ein Common-Rail-System der Firma Bosch mit einer Einkolbenpumpe CP 4.1 und Piezoinjektoren. Da bei diesen Anlagen gelegentlich die Piezoinjektoren an der Düsennadel undicht werden und dann der Raildruck zusammenbricht, riet ich ihm, die Injektoren auf Dichtigkeit zu prüfen.
Häufig ist der Fehler auch schon bei der Mengenabweichung im Leerlauf zu sehen. Einige Tage später berichtete er, dass der Austausch eines verdächtigen Injektors nicht weitergeholfen hatte. So einfach war der Fehler also nicht zu beheben.
Ich packte meine Messgeräte ein und wir starteten mit einer Probefahrt, um Soll- und Istwerte des Raildrucks aufzuzeichnen (Bild unten). Bei Raildrücken unter 1.500 bar lief der Motor normal. In der Aufzeichnung konnte man gut sehen, dass bei Raildrücken über 1.500 bar der Istwert ungefähr 200 bar über dem Sollwert lag. Daraufhin begrenzte das Steuergerät den Raildruck auf 1.200 bar, um Schäden in der Anlage zu vermeiden.