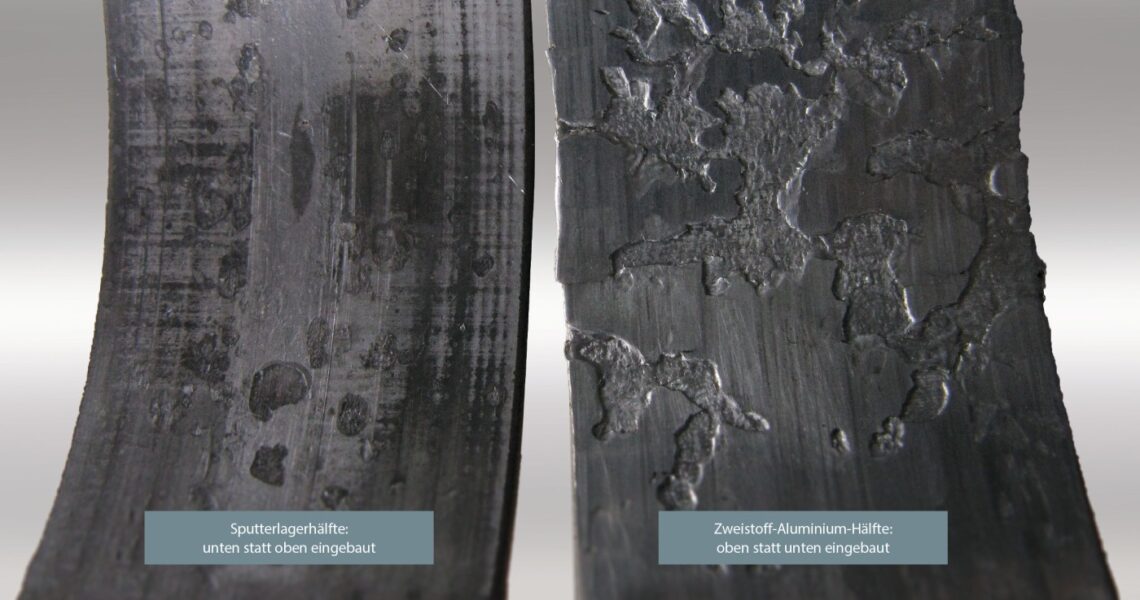
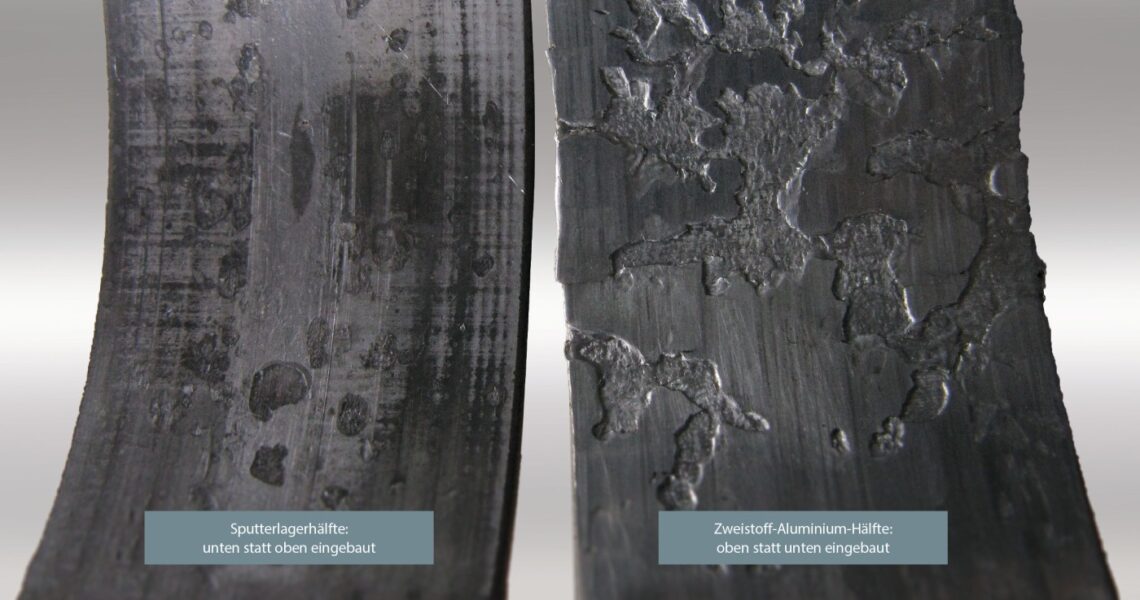
Da die Leistungsdichte moderner Motoren stetig steigt, nimmt auch die spezifische Belastung – also die Lagerkraft bezogen auf die Lagerfläche – für die Haupt- und Pleuellagerung zu. Um dieser standzuhalten, müssten auch die Abmessungen der Lager wachsen – tun sie zumeist aber nicht. Ein Experte hat KRAFTHAND erklärt, warum das so ist und worauf bei der Instandsetzung zu achten ist.
Kompensiert ein Motorenhersteller die steigenden Belastungen, die auf einen Verbrennungsmotor einwirken, damit, dass er die Abmessungen der Lager vergrößert, erhöhen sich sowohl das Gewicht der Kurbelwelle als auch die Reibverluste des Motors. Um bei gleichbleibenden Abmessungen den hohen Belastungen standzuhalten, wurden deshalb spezielle Lagerwerkstoffe und Oberflächenbehandlungen entwickelt, die sehr hohe Flächenpressungen tolerieren.
Laut Richard Wild, Inhaber von Wild Motoren, setzen die Hersteller bei solchen hochbelasteten Motoren für die stärker belastete Pleuellagerhälfte meist ein Sputter-Dreistofflager ein. Deren nur wenige Mikrometer dicke Laufschicht weist dabei eine sehr hohe Oberflächenhärte auf und hält hohe Pressungen aus.
In vielen Fällen ist die Einbaurichtung schon optisch an der Gleitlageroberfläche erkennbar.
Das Kathodenzerstäuben, kurz „Sputtern“ (engl. to sputter = zerstäuben) ist eine Dünnschichttechnologie aus der Klasse der PVD-Verfahren (Physical Vapour Deposition). Dabei wird das abzuscheidende Material (Sputtertarget) durch Beschuss mit Plasma-Ionen zunächst zerstäubt und in die Gasphase überführt. Auf dem zu beschichtenden Substrat kondensiert anschließend dieser Teilchendampf als hauchdünne, fest haftende Schicht.