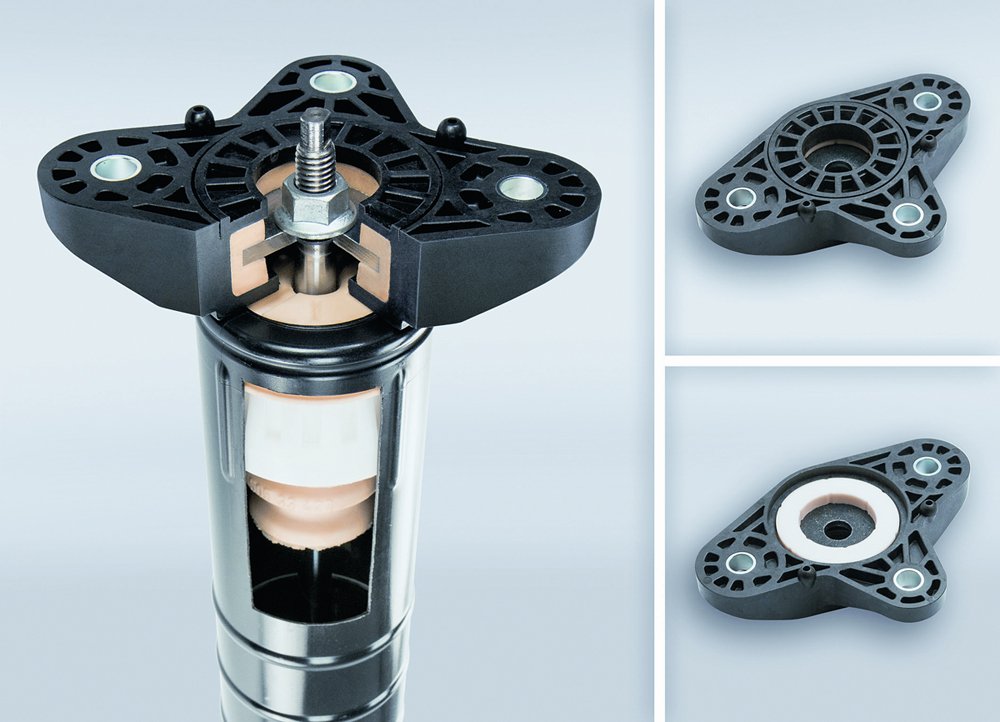
Die BASF baut ihre Kompetenz bei Dämpferlagern aus, um Automobilherstellern eine optimale Kombination aus Gewichtsersparnis, Akustik und Schwingungsdämpfung zu ermöglichen. Realisierbar wird die neue NVH-Lösung (NVH: Noise, Vibration, Harshness) durch die Verbindung zweier BASF-Kunststoffspezialitäten: dem mikrozelligen Polyurethan-Elastomer ‚Cellasto’ und dem hochglasfaserverstärkten Polyamid ‚Ultramid A3WG10 CR’.
Das Dämpferlager mit dem Cellasto-Element und dem Ultramid-Gehäuse ist Unternehmensangaben zufolge rund 25 Prozent leichter als gängige Aluminiumdruckguss-Versionen mit Gummi.
Das Dämpferlager verbindet den Stoßdämpfer mit der Karosserie und hat somit maßgeblichen Einfluss auf Fahrkomfort und Fahrdynamik. Deshalb ist das Materialzusammenspiel der einzelnen Komponenten von entscheidender Bedeutung: Cellasto zeigt Produktangaben zufolge ein optimales statisches und dynamisches Verhalten, hat eine lange Lebensdauer und beansprucht wenig Bauraum. Die PA66-Type ‚Ultramid A3WG10 CR’ ist mit 50 Prozent Glasfasern verstärkt und deshalb besonders steif und fest, auch bei hohen Temperaturen. Der technische Kunststoff eignet sich besonders für dynamische Lasten und ist damit eine Alternative zu Metall.
Dämpferlager
Zum Dämpferlager kombiniert lassen sich Unternehmensangaben zufolge so das eigentliche Lager, die Zusatzfeder und das Schutzrohr des Stoßdämpfers funktional integrieren sowie eine sehr gute Dämpfung und Akustik erzielen. Mit einer von der BASF entwickelten Fertigungstechnologie werden Gehäuse und Lagerelement dauerhaft verbunden.