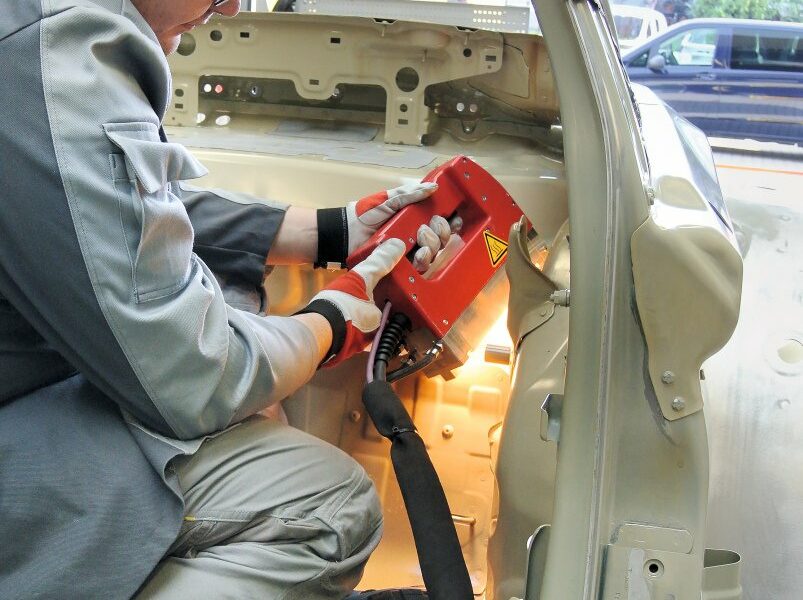
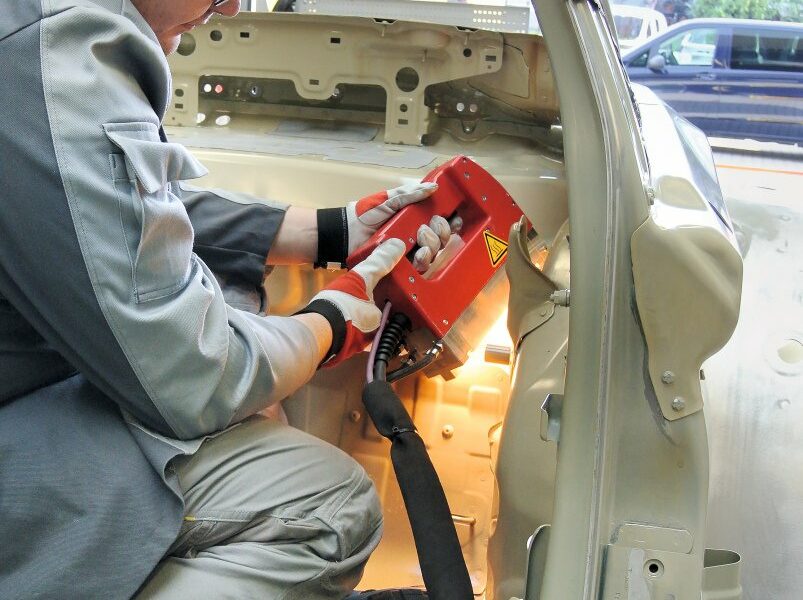
Aus dem modernen Karosserieleichtbau ist die Klebetechnik nicht mehr wegzudenken. Grund ist ein ausgeklügelter Multi-Materialmix, der leichtere, kraftstoffsparendere Autos ermöglicht. Bei der Reparatur solcher gewichtsoptimierten Karosserien ist jedoch spezielles Know-how und Equipment gefragt, etwa um Klebeverbindungen fachgerecht zu lösen.
Nicht nur bei Sportwagen kämpfen die Ingenieure um jedes Gramm. Auch bei ganz normalen Alltagsautos ist konsequenter Leichtbau angesagt – insbesondere im Karosseriebau. Denn weniger Gewicht spart Sprit und wirkt sich positiv auf Beschleunigung, Fahrstabilität oder Bremsweg aus. Dabei geht der Trend unaufhaltsam zum intelligenten Multi-Materialmix mit verschiedenen Stahlsorten, Aluminium, Kunststoff, Magnesium, Carbon und Faserverbundstoffen.
Damit wird aber nicht nur die Fertigung beim Fahrzeughersteller komplexer, sondern auch die Reparatur in der Werkstatt. Denn neue Technologien erfordern im Schadensfall meist zwangsläufig neue Diagnose- und Instandsetzungsverfahren. Außerdem gestaltet sich die Reparatur aufgrund der neuen Fügeverfahren deutlich anspruchsvoller. Genügt zur Diagnose eines Unfallschadens bei konventionellen Stahlkarosserien üblicherweise die Kontrolle mittels Messlehren auf der Richtbank, verlangt eine Multi-Materialmix-Karosserie laut Porsche schon bei leichten bis mittleren Schäden eine digitale Vermessung mit einem elektronischen Messsystem mit sehr geringen Messtoleranzen. Diese liegen etwa bei Porsche aktuell bei +/– 1 mm, im Gegensatz zu den früher üblichen +/– 5 mm.
Darüber hinaus wird bei modernen gewichtsoptimierten Karosserien zunehmend geklebt und genietet statt geschweißt. Und das nicht nur im Sportwagenbau: Selbst in vielen „Brot-und-Butter“-Autos sind mittlerweile 15 kg und mehr Kleber verarbeitet, was einer Klebenahtlänge von etwa 130 bis 160 m entspricht.
Der Aufschwung der Klebetechnik im Fahrzeugbau begann Ende der 90er Jahre. Die Vorteile sind unter anderen:
Anfangs meist nur punktuell eingesetzt, gestatten seit der Jahrtausendwende speziell flexibilisierte und hochfeste Klebstoffe zunehmend auch crashstabile Strukturverklebungen. Diese neuartige Klebergeneration verbessert die Karosseriesteifigkeit deutlich und erhöht durch ein größeres Energieaufnahmevermögen der geklebten Bauteile auch die Crashstabilität. Da es sich bei den in der Produktion eingesetzten, chemisch aushärtenden Klebern um fließfähige, niedrigviskose Stoffe ohne Anfangsfestigkeit handelt, müssen die Bauteile zusätzlich noch mechanisch fixiert werden. Deshalb kombinieren die Autobauer das Strukturkleben in vielen Bereichen mit thermischen und/oder mechanischen Fügeverfahren wie Punktschweißen, Clinchen, Blindnieten, Stanznieten, spezielle Flow-Drill-Schrauben etc. – deshalb spricht man von Hybridverklebungen.
Während es sich am Band üblicherweise um Einkomponenten-Strukturklebstoffe handelt, die überwiegend unter hohen Temperaturen aushärten, verwendet man bei Reparaturen mittlerweile spezielle crashstabile Zweikomponenten-Strukturklebstoffe, deren Eigenschaften nahezu jenen von Originalklebstoffen entsprechen und somit eine fachgerechte Instandsetzung in der Werkstatt erlauben. Obschon die Reparaturklebstoffe nicht erwärmt werden müssen, um auszuhärten, fehlt auch diesen die Anfangsfestigkeit, so dass im Reparaturfall vielfach ebenfalls noch zusätzliche thermische oder mechanische Fügeverfahren notwendig sind.
Hybridkleben, also die Kombination von Strukturkleben mit Blind- oder Stanznieten, wird mittlerweile bei der Karosseriereparatur sehr häufig praktiziert und ersetzt das rein thermische Fügen. Immer mehr Fahrzeughersteller gehen dazu über, Heckabschlussbleche, Seitenwände, Dachaußenhäute und auch Strukturbereiche wie Verstärkungsbleche von B-Säulen, Längsträger-Teilstücke oder Stützträger „kalt“ zu fügen. Sprich: mittels Klebetechnik instandzusetzen. Zu den Wegbereitern auf diesem Gebiet gehört zweifelsohne BMW, wo das Reparaturkonzept „Kleben und Nieten“ mittlerweile für alle aktuellen Modelle gilt, die mit Stahlkarosserie vom Band laufen.
Die kalte Instandsetzung vereinfacht nicht nur den Reparaturvorgang an sich, sondern reduziert die Durchlaufzeiten in den Karosserie- und Lackabteilungen insgesamt, denn einerseits fallen Rüstzeiten aufgrund des geringeren Rüstumfangs kürzer aus, andererseits fallen weniger schweißbedingte Kollateralschäden an, etwa um den Korrosionsschutz wiederherzustellen. Denn bei der Klebetechnik wird dieser durch die flächig verklebte Reparaturstelle gewährleistet. Darüber hinaus bleibt die werkseitige kathodische Tauchlackierung (KTL) der Karosserie und des Ersatzteils weitestgehend erhalten. Außerdem wird das Gefüge thermisch sensibler Materialien wie hoch-, höher- oder höchstfester Stahlbleche nicht durch die eingebrachte Wärme beeinflusst oder gar negativ verändert, noch verwerfen sich die Bleche in den Verbindungsbereichen. Allerdings sind für die fachgerechte kalte Instandsetzung entsprechende Kenntnisse und spezielle Werkstattausrüstung unumgänglich – was Investitionen in Schulung und Equipment erfordert.
Besonders die werkseitigen Klebenähte gehören bei der Unfallschadenreparatur zu den besonderen Herausforderungen für Blechprofis. Denn bei Abschnittsreparaturen müssen nicht nur Punktschweißpunkte und Nieten ausgebohrt, sondern auch die Klebeverbindungen „geöffnet“ werden. Dazu ist gezielter Wärmeeinsatz notwendig. Doch die offene Flamme eines Schweißbrenners verbietet sich hierbei aus Korrosionsschutzgründen ebenso wie der rohe Einsatz eines Blechmeißels, um die verklebten Bleche zu trennen. „Der Heißluftfön ist hierfür nur bedingt geeignet. Zum einen dauert es sehr lange, um damit den Kleber so weit zu erwärmen, bis er nur noch eine geringe Restfestigkeit hat und sich die Bleche lösen lassen. Zum anderen hat der Mechaniker in engen Arbeitssituationen mit der Abwärme zu kämpfen“, berichtet Stefan Kopietz, Geschäftsführer von Cebotech (www.cebotech.de), ein auf Schweißtechnik und Ausbeulsysteme spezialisiertes Unternehmen.