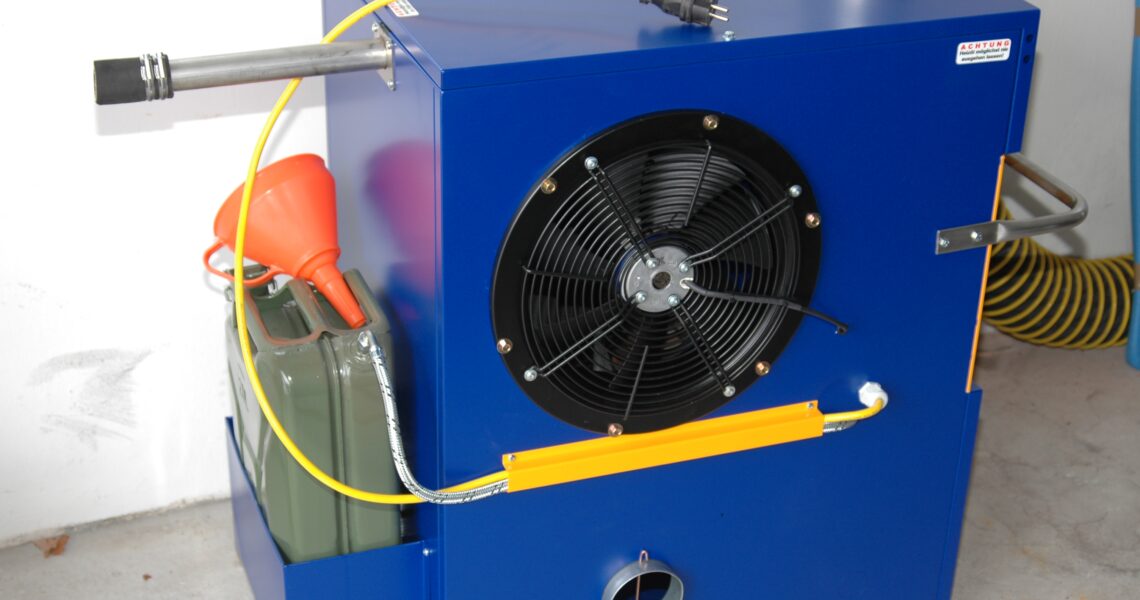
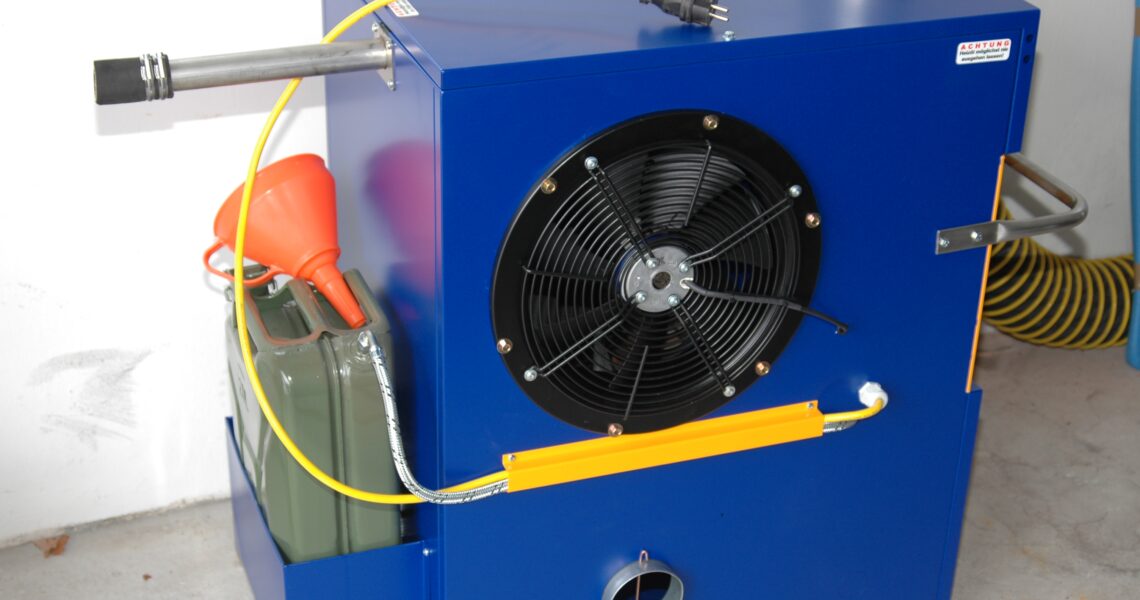
KRAFTHAND erhielt für die KRAFTHAND-Werkstatt vom österreichischen Spezialisten Pletzer ein Warmluft-Werkstatt-Heizgerät in der Standardversion mit einer Leistung von 18 kW zum Testen.
Georg Pletzer ist mit seinen Puls-Air-Heizgeräten seit 15 Jahren auf dem Markt und hat eigenen Angaben zufolge bisher rund 1.300 Stück der im Eigenbau hergestellten Produkte abgesetzt. Im Gegensatz zu den bisher üblich eingesetzten Öl- und Gasbrennern mit kontinuierlicher Verbrennung wird bei diesem Heizgerät ein (bereits vergessenes) neuentdecktes und pulsierendes Verbrennungsverfahren angewendet. Dafür erhielt das Unternehmen den Bayerischen Staatspreis.
Bei diesem System entsteht während des Betriebs eine schwingende Gassäule im ‚Auspuffrohr’ zwischen Brennkammer und Schwingungsentkoppler. Dabei wechselt das Gas zirka 62-mal in der Sekunde seine Strömungsrichtung, und genauso oft wechselt auch der Druck in der Brennkammer zwischen Unterdruck und Überdruck. Dadurch sind die Brennstoffteilchen wesentlich besser aufgeschlossen und die Abgasemissionsbildung wird drastisch reduziert. Laut eigenen Angaben kommt es bei dieser Verbrennungsart zu einer nahezu ruß- und rückstandsfreien Verbrennung.
Wenn einmal der richtige Standort in der Werkstatt festgelegt ist, gestaltet sich das Aufstellen des steckerfertigen Heizgerätes anhand der ausführlichen Betriebsanleitung sehr einfach. Das Gerät muss immer am Boden des zu beheizenden Raumes stehen. Sollte der Ventilator zur Gebäudewand weisen, ist ein Mindestabstand vom Ventilator zur Wand von 300 mm einzuhalten. Das Gerät arbeitet nach dem Umluftprinzip, das heißt, die Raumluft erwärmt sich und wird im vorgewärmten Zustand vom Lüfter angesaugt und nochmals erwärmt wieder in den Werkstattraum geblasen. Somit erwärmen sich die Räumlichkeiten sehr schnell.
Als Brennstoff darf der Anwender nur extraleichtes Heizöl verwenden. Der mitgelieferte und an der Geräteseite befestigte Brennstoffkanister ist bereits mit 20 l Dieselkraftstoff befüllt. Der Behälter sollte vor Schmutz und Staub geschützt werden, sodass keine Schmutzpartikel in den Tank gelangen. Zum Nachfüllen des Kanisters ist der ebenfalls mitgelieferte Trichter mit Sieb zu benützen. Der Werkstattprofi sollte den Brennstoff möglichst nie ausgehen lassen, sondern rechtzeitig nachfüllen, um eventuelle Störungen zu vermeiden. Den Heizöltank außerdem niemals in der Kälte im Freien lagern: Heizöl stockt bei Temperaturen unter – 6 °C und das Heizgerät lässt sich dann nicht mehr starten.
Das Auspuffrohr kann in einen bestehenden Kamin eingeleitet werden. Wo kein Kamin vorhanden ist, sind die Abgase problemlos mit einem passenden Edelstahlrohr (Außendurchmesser 35 mm, innen 32 mm) oder Metallschlauch wie auch einem Gummi-Abgas-Schlauch ins Freie zu leiten. Dadurch ist immer abgasfreie Warmluft im Werkstattraum. Das Rohr muss vom Heizgerät weg leicht fallend verlaufen, damit eventuelles Kondenswasser nicht zum Gerät zurückfließen und Störungen verursachen kann.
Der Start erfolgt auf Schalterstufe zwei, nach rund fünf Minuten kann der Werkstattprofi auf Stufe eins zurückschalten. Der Brennstoffverbrauch und die Heizleistung sind in dieser Sparstufe um rund 30 Prozent verringert. Beim Ausschalten des Gerätes ist zu beachten, nur den Ein-/Ausschalter zu verwenden. Auch niemals bei laufendem Gerät den Stecker herausziehen, da sonst wegen Überhitzung die Übertemperatur-Sicherung ‚herausspringt’! Nach dem Abschalten des Heizgerätes läuft der Ventilator noch weiter und schaltet sich nach rund drei Minuten selbstständig ab. In der anschließenden Abkühlphase schaltet er sich noch zirka zweimal ein und aus.
Puls-Air-Geräte sind in der Standardversion – bei voller Leistung stehen hier 18 kW für Werkstatträume bis maximal 600 m3 bereit – und als leistungsstärkere Variante für Räume bis maximal 1.000 m3 mit 21 kW Leistung erhältlich. Beide Versionen werden an ein herkömmliches 220-V-Netz angeschlossen. In unserer KRAFTHAND-Profi-Werkstatt herrschte mit dem Standard-Heizgerät nach rund zwei Stunden Betrieb eine angenehme Arbeitstemperatur. Das leise Arbeitsgeräusch und der niedrige Heizölverbrauch überzeugten dabei.
Pulsotriebwerke sind Strahltriebwerke, die mit einer pulsierenden Verbrennung arbeiten. Ihre Wirkungsweise beruht auf dem Rückstoßprinzip. Erstmals schlug der Franzose Marconnet 1909 Strahltriebwerke mit dieser Verbrennung vor. Der Münchner Paul Schmidt erhielt 1930/31 grundlegende Patente auf Konstruktionspläne derartiger Triebwerke, die als so genannte ‚Schmidt-Rohre’ gebaut wurden.
Hier strömt Luft durch Rückschlagventile in die Brennkammer. Dort wird sie mit Brennstoff vermischt, gezündet und verbrennt explosionsartig. Durch den Explosionsdruck schließen die Rückschlagventile.
Die Verbrennungsgase strömen dann mit hoher Geschwindigkeit durch das offene Rohrende – die Schubdüse – ins Freie und erzeugen den gewünschten Schub. Beim Ausströmen der Verbrennungsgase entsteht im vorderen Teil der Kammer ein Unterdruck, der die Ventile öffnet. Frischluft und Brennstoff werden erneut angesaugt. Gleichzeitig baut sich vom Rohrende her eine Druckwelle auf. Sie verdichtet das Brennstoff-Luft-Gemisch und zündet es durch heiße Restgase. Die Zündung erfolgt in bestimmten Abständen, die hauptsächlich von der Rohrlänge abhängen. Die Pulso-Strahltriebwerke verbrauchen viel Brennstoff, sind jedoch sehr leicht und billig in der Herstellung.
Der Konstrukteur und Entwickler der Puls-Air-Heizgeräte Georg Pletzer wurde von der Military-Aircraft-Division der Firmen Messerschmitt-Bölkow-Blohm und der US-Firma Teledyne Brown Engineering mit der Entwicklung von Pulso-Jet-Strahltriebwerken als Antrieb für unbemannte militärische Zielflugkörper beauftragt. Die Triebwerke mit 16 kg Eigengewicht und 104 kp Standschub hat man im Windkanal der Universität Stuttgart bei Geschwindigkeiten bis Mach 0,7 – das sind 854 km/h – erfolgreich erprobt. Das bei diesen Triebwerken angewandte Verbrennungsprinzip kommt auch in den ‚friedlichen’ Heizgeräten zum Einsatz. Vom Beginn der Entwicklungsarbeiten bis zur endgültigen Verfügbarkeit der Heizgeräte vergingen rund sechs Jahre, die Entwicklungskosten betrugen zirka 4 Mio. Schilling.