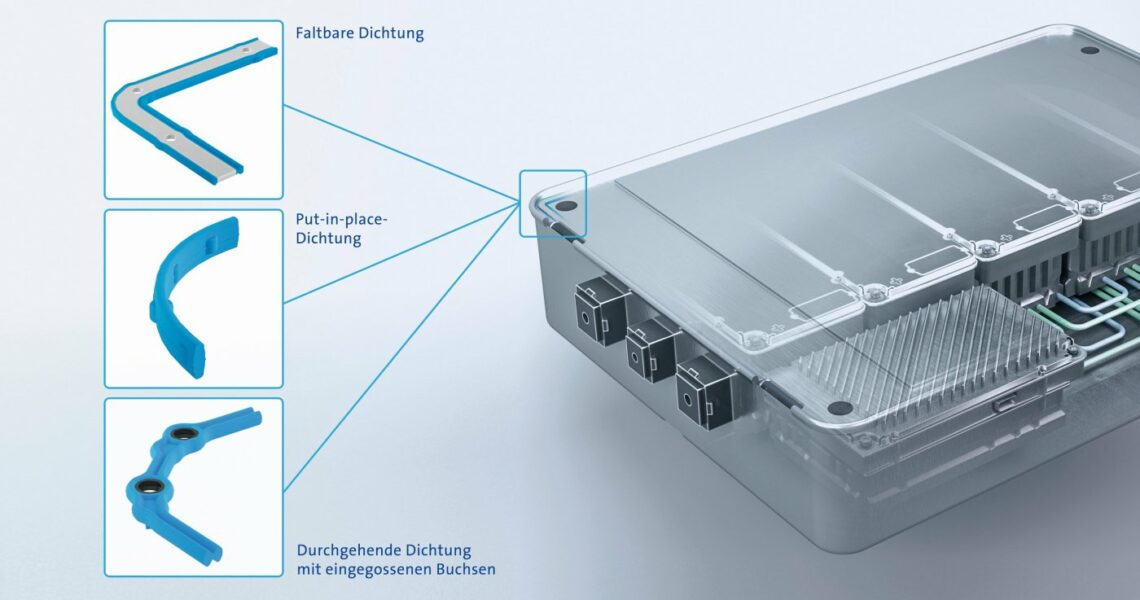
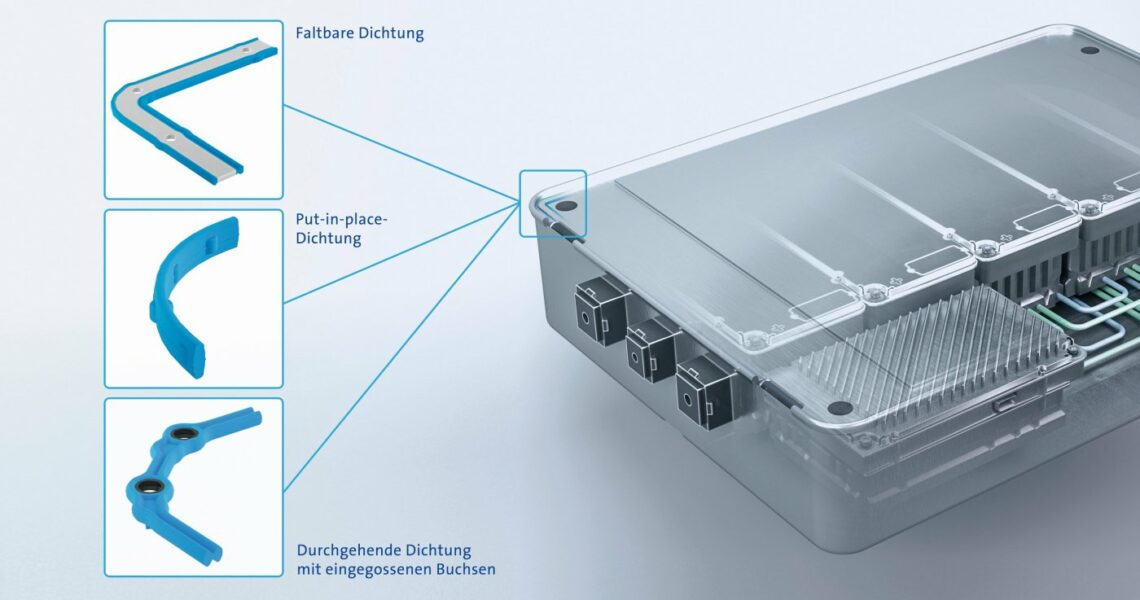
Das Ziel der Hersteller von Elektroautos ist eine immer höhere Reichweite. Das schaffen sie durch immer leistungsdichtere Batterien. Doch je größer und damit energiereicher der Akku ausfällt, desto wichtiger wird es, ihn sicher abzudichten.
Zum einen damit weder Spritzwasser noch Schmutz eindringen kann, zum anderen, um bei einem Brand über einen längeren Zeitraum zu verhindern, dass sich das Feuer ausbreitet. Die Ingenieure von Freudenberg Sealing Technologies haben dafür mehrere Lösungen entwickelt.
Wie in der Luftfahrtindustrie werden auch die Akkudichtungen für Elektroautos sogenannten Flammenausbreitungstests unterzogen. Bei diesen Tests wird eine Materialprobe einer Flamme mit einer definierten Temperatur ausgesetzt und anschließend deren Ausbreitungsgeschwindigkeit gemessen. Anhand der Geschwindigkeit wird der Werkstoff klassifiziert. Mit einer neuen Materialmischung erreicht Freudenberg die höchste Klasse V0 – nach zehn Sekunden Testdauer erlischt die Flamme vollständig.
Ob eine Dichtung einen Brand für den gewünschten Zeitraum übersteht, hängt aber auch von der korrekten Montage ab. Freudenberg bietet deshalb mehrere Dichtungsvarianten an, bei denen Fehlmontagen ausgeschlossen sind. Beispielsweise die faltbare Dichtung (siehe Bild) als Gesamtbauteil. Sie hat feste, an der Außenkante mit einem Dichtungsprofil versehene Aluminiumelemente mit Aufnahmepunkten für die Clips, mit denen die Dichtung am Gehäusedeckel befestigt wird.
Die Elemente sind unter einander mit einem durchlaufenden hoch flexiblen Dichtungsprofil verbunden, das sogar kleine Fertigungstoleranzen des Gehäuses ausgleichen kann. Die metallischen Einlagen stellen zudem eine hohe elektrische Leitfähigkeit zwischen Batteriegehäuse und Deckel sicher und schirmen somit elektromagnetische Felder effizient ab.
Für großformatige Batterien gibt es ein durchgängiges Elastomerbauteil mit eingegossenen metallischen Buchsen, welche die Festigkeit und elektrische Leitfähigkeit sicherstellen. Die Befestigungselemente sind ebenfalls eingegossen, was definierte Aufnahmepunkte und damit ebenfalls eine hohe Montagesicherheit ermöglicht. Den Einbau von sehr großen Batterien kann so ein einzelner Mitarbeiter bewerkstelligen.
Der Dichtungsspezialist hat zudem ein eigenes Verfahren für Dauerprüfungen entwickelt, das ermöglicht, die Dichtungen ohne reales Gehäuse zu testen. Mit einem Hydropulser, der mit einer Frequenz von bis zu 50 Hertz auf ein aus zwei Hälften bestehendes und abgedichtetes Testgehäuse einwirkt, können die Verwindungen simuliert werden, die im realen Straßenbetrieb auftreten. Im Inneren des Gehäuses herrscht permanent ein leichter Überdruck, so dass Leckagen sicher entdeckt werden. Die gesamte Testeinrichtung befindet sich in einer Klimakammer, um Temperatureinflüsse erfassen zu können.